T.O. 1-1A-9
e.
304L-Carbon (c) lowered for welding applications.
f.
309-Cr and Ni higher for additional corrosion and scale resistance.
g.
316-Molybdenum (Mo) added to improve corrosion resistance and strength.
h.
316L-Clowered for welding applications.
i.
321-Titanium (Ti) added to reduce/ avoid carbide precipitation (stabilized grade).
j.
347-Columbium(Cb), Tantalum (Ta) Added to reduce/avoid carbide precipitation (stabilized grade).
k.
347F or Se Sulfur(s) or Selenium (Se) added to improve machinability.
The chrome-nickel steels are used for a variety of applications on aircraft and missiles. In plate and sheet form it is used
for fire walls, surface skin, exhaust stacks, heater ducts, gun wells, ammunition chutes, clamps, heat shields/deflectors,
fairing, stiffeners, brackets, shims, etc. In bar and rod it is used to fabricate various fittings, bolts, studs, screws, nuts,
couplings, flanges, valve stems/seats, turn-buckles, etc. In wire form it is used for safety wire, cable, rivets, hinge pins,
screens/screening and other miscellaneous items.
2-11. CHROME-VANADIUM STEELS. The vanadium content of this steel is approximately 0.181percent and the
chromium content approximately 1.00 percent. Chrome vanadium steels when heat-treated have excellent properties
such as strength, toughness, and resistance to wear and fatigue. A special grade of this steel in sheet form can be cold-
formed into intricate shapes. It can be folded and flattened without signs of breaking or failure. Chrome-vanadium steel
with medium high carbon content (SAE 6150) is used to make springs. Chrome-vanadium steel with high carbon content
(SAE 6195) is used for ball and roller bearings.
2-12. CHROME MOLYBDENUM STEELS. Molybdenum in small percentage is used in combination with chromium to
form chrome molybdenum steel; this steel has important applications in aircraft. Molybdenum is a strong alloying
element, only 0.15 to 0.25 percent being used in the chrome-molybdenum steels; the chromium content varies from 0.80
to 1.10 percent. Molybdenum is very similar to tungsten in its effect on steel. In some instances it is used to replace
tungsten in cutting tools, however; the heat treat characteristic varies. The addition of up to 1% molybdenum gives steel
a higher tensile strength and elastic limit with only a slight reduction in ductility. They are especially adaptable for
welding and for this reason are used principally for welded structural parts and assemblies. Parts fabricated from 4130,
are used extensively in the construction of aircraft, missiles, and miscellaneous GSE equipment. The 4130 alloy is used
for parts such as engine mounts (reciprocating), nuts, bolts, gear structures, support brackets for accessories, etc.
2-13. PRINCIPLES OF HEAT TREATMENT OF STEELS.
2-14. HARDENING. At ordinary temperatures, the carbon content of steel exists in the form of particles of iron carbide
scattered throughout the iron matrix; the nature of these carbide particles, i.e., their number, size, and distribution,
determines the hardness and strength of the steel. At elevated temperatures, the carbon is dissolved in the iron matrix
and the carbide-particles appear only after the steel has cooled through its "critical temperature" (see next paragraph).
If the rate of cooling is slow, the carbide particles are relatively coarse and few; in this condition the steel is soft. If the
cooling is rapid, as be quenching in oil or water, the carbon precipitates as a cloud of very fine carbide particles, which
condition is associated with high hardness of the steel.
2-3
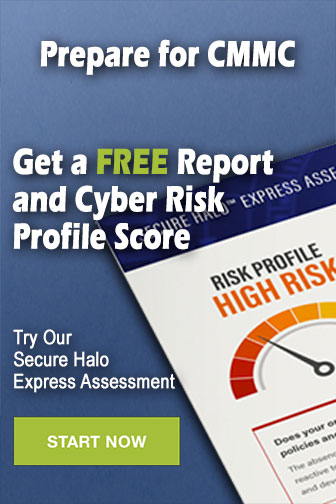