T.O. 1-1A-9
HEAT TREATMENT. An operation, or combination of operations, involving the heating and cooling of a metal or alloy in
the solid -state for the purpose of obtaining certain desirable conditions or properties. Heating and cooling for the sole
purpose of mechanical working are excluded from the meaning of this definition.
HOMOGENIZING. Annealing or soaking at very high temperatures in order to reduce alloy segregation by diffusion.
HOT SHORTNESS. Brittleness in metal when hot. In iron when sulphur is in excess of the manganese necessary to
combine with it to form manganese sulphide the excess sulphur combines with the iron to form iron sulphide. This
constituent has a lower melting point than the iron and the result can be that steel may crack during hot working.
HYDROGEN EMBRITTLEMENT. See Acid Brittleness.
IMPACT TEST. A test in which one or more blows are suddenly applied to a specimen. The results are usually
expressed in terms of energy absorbed or number of blows (of a given intensity) required to break the specimen. See
Charpy Impact and Izod Impact.
INCLUSION. Particles of impurities, usually oxides, sulphides, silicates, and such which are mechanically held during
solidification or which are formed by subsequent reaction of the solid metal.
INDUCTION HARDENING. A process of hardening a ferrous alloy by heating above the transformation range by means
of electrical induction and then cooling as required.
MACHINABILITY. The cutting characteristic of metal and resulting surface finish using standard cutting tools and
coolant/lubricants. There are various factors that effect the machinability of a metal such as hardness, grain size, alloy
constituents, structure, inclusions; shape, type, condition of tool and coolant. The standard machinability ratings are
usually based on comparison to SAE 1112/Aisi B 1112 Bessemer screw stock which is rated at 100% machinability.
MAGNAFLUX TESTING. A method of inspection used to detect/locate defects such as cavities, cracks or seams in
steel parts at or very close to the surface. The test is accomplished by magnetizing the part with equipment specially
designed for the purpose and applying magnetic powder, wet or dry, Flaws are then indicated by the powder clinging to
them (see Section VIII for additional data).
MALLEABILITY. Malleability is the property of a material which enables it to be hammered, rolled, or to be pressed into
various shapes without fracture. Malleability refers to compression deformation as contrasted with ductility where the
deformation is tensile.
MARTEMPERING. This is a method of hardening steel by quenching from the austenitizing temperature into a medium
at a temperature in the upper part of or slightly above the martensite range and holding it in the medium until
temperature is substantially uniform throughout the alloy is then allowed to cool in air through the martensite range.
MARTENSITE. It is the decomposition product which results from very rapid cooling of austenite. The lower the carbon
content of the steel, the faster must be cooling to obtain martensite.
MECHANICAL HARDNESS. See Hardness.
MECHANICAL PROPERTIES. Those properties that reveal the reaction, elastic and inelastic, of a material to an applied
force, or that involve the relationship between stress and strain; for example, tensile strength, yield strength, and fatigue
limit.
MECHANICAL TESTING. Testing methods by which mechanical properties are determined.
MECHANICAL WORKING. Subjecting metal to pressure exerted by rolls, presses, or hammers, to change its form, or to
affect the structure and therefore the mechanical and physical properties.
MODULUS OF ELASTICITY. The ratio, within the limit of elasticity, of the stress in the corresponding strain. The stress
in pounds per square inch is divided by the elongation in fractions of an inch for each inch of the original gage length of
the specimen.
NITRIDING. Adding nitrogen to iron-base alloys by heating the metal in contact with ammonia gas or other suitable
nitrogenous material. Nitriding is conducted at a temperature usually in the range 50205380C (9350-10000F) and
produces surface hardening of the metal without quenching.
NORMALIZING. Heating iron-base alloys to approximately 550°C (100°F) above the critical temperature range, followed
by cooling to below that range in still air at ordinary temperatures. This process is used to remove stresses caused by
machining, forging, bending, and welding.
1-6
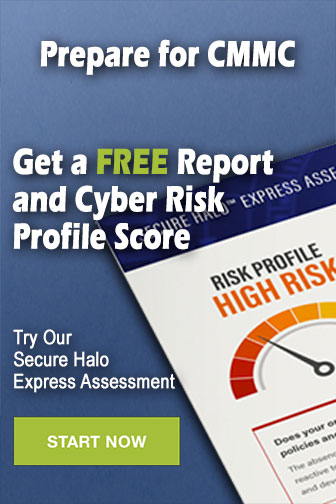