T.O. 1-1A-9
DECALESCENCE. When a piece of steel is heated, the temperature rises uniformly until it reaches a point between
7180C and 732oC (1,325OF and 1,350°F). At this point the rise in temperature suddenly halts due to the fact that the
metal absorbs the heat necessary for the change of state. After this halt the temperature will continue its normal rate of
increase. It is the halting in the temperature range that is termed decalescence. At the point of decalesence, the carbon
and iron are forming a solid solution and the steel is passing from its annealed condition into its hardened condition.
DECARBURIZATION. The removal of carbon (usually refers to the surface of solid steel) by the (normally oxidizing)
action of media which reacts with carbon.
The decarburized area is sometimes referred to as the bark.
DEFECTS IN METALS. Damage occurring to metal during manufacture/fabrication process. Some typical defects are
as follows:
a.
Blister a defect in metal produced by gas babbles either on the surface or formed beneath the surface. Very fine
blisters are called pinhead or pepper blisters.
b.
Blow hole a hole produced during the solidification of metal by evolved gas which in -tiling to escape, is held in
pockets.
c.
Bursts ruptures made in forging or rolling.
d.
Fin (Flash) a thin fin of metal formed at the side of a forging or weld where a small portion of the metal is forced
out bet-en the edges of the forging or welding case.
e.
Flake Internal fissures (cracks or clefts) in large steel forging or large (A88) rolled shapes. In a factured surface
or test piece, they appear as sizable areas silvery brightness and coarser grain size thin their surroundings. Sometimes
known a "chrome checks" and "hairline cracks."
f.
Ghost (Ferrite ghost) a faint bud of ferrite.
g.
Lap surface defect appearing as seam caused from folding over hot metal, fine, or sharp corners and then rolling
or forging, but not welding, them into the surface.
h.
Pipe a cavity formed in metal (especially ingot) during solidification of the last portion of liquid metal causes the
cavity or pipe.
i.
Scab a rough projection on a casting caused by the mold breaking or being washed by the molten metal; or
occurring where the sin from a blowhole has partly burned away and is not welded.
J.
Seam a crack on the surface of metal which has been closed but not welded; usually produced by blowholes
which have become oxidized. If very fine, a seam may be called a hair crack or hair seam.
k. Segregation a mixture of compounds and elements, which, when cooled from the molten state, solidify at
different temperatures.
l.
Ductility the ability of a metal to withstand plastic deformation without rupture. Ductility is usually determined by
tension test using a standard test (2" gauge length) specimen. The test specimen is loaded in tension to rupture. The
specimen is then assembled and measured for length and diameter at the fracture. The increase in length is expressed
as per cent elongation and the decrease in diameter as per cent reduction of area. The above terms measure ductility
and since they are comparative, considerable experience is required for proper evaluation of material for the purpose
intended.
DUCTILITY. The property that permits permanent deformation before fracture by stress in tension.
ELASTIC LIMIT. The elastic limit of a material is the greatest load per unit area which will not produce a measurable
permanent deformation after complete release of load.
ELONGATION. The amount of permanent extension at any stage in any process which continuously elongates a body.
EMBRITTLEMENT. Loss of ductility of a metal, which may result in premature failure. (see acid brittleness).
ENDURANCE LIMIT. The highest unit stress at which a material can be subjected to a very large number of repetitions
of o loading and still show no evidence of failure. Above this limit failure occurs by the generation and growth of cracks
until fracture results in the remaining section.
ENDURANCE RATIO. The ratio of the endurance limit for cycles of reversed flexural stress to the tensile strength.
EQUALIZING. intermediate heat treatment (special) which assists i developing desired properties, primary use is for
equalizing/relieving stresses resulting from cold working.
EUTECTIC ALLOY. An alloy which has a lower melting point than neighboring compositions. More than one eutectic
composition may occur in a given all by system.
EXFOLIATION. The cracking or flaking off of the outer layer of an object.
1-4
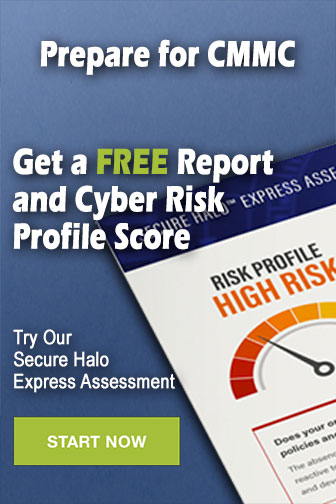