T.O. 1-1A-9
OVERHEATING. Heating to such high temperatures that the grains have become coarse, thus impairing the properties
of the metal.
PATENTING. Heating iron-base alloys above the critical temperature range followed by cooling below that range in air,
or in molten lead, or a molten mixture of nitrates or nitrites maintained at a temperature usually between 427°-5660C
(800°-10500F), depending on the carbon content of the steel and the properties required of the finished product. This
treatment is applied to wire and to medium or high carbon steel as a treatment to precede further wire drawing.
PHYSICAL PROPERTIES. Those properties exclusive of those described under mechanical properties; for example,
density, electrical conductivity, coefficient of thermal expansion. This term has often been used to describe mechanical
properties, but this usage is not recommended.
PHYSICAL TESTING . Testing methods by which physical properties are determined. This term is also in advisedly
used to mean the determination of the mechanical properties.
PICKLING. Removing scale from steel by immersion in a diluted acid bath.
PLASTIC DEFORMATION . The permanent change in size or shape of a material under stress.
POTENTIOMETER. Potentiometer is an instrument used to measure thermocouple voltage by balancing a known
battery voltage against it.
PROCESS ANNEALING. Heating iron-base alloys to a temperature below or close to the lower limit of the critical
temperature range, followed by cooling as desired. This treatment is commonly applied to sheet and wire and the
temperatures generally used are from 5490 to 6490C (10200to 1200°F).
PROOF STRESS. The proof stress of a material is that load per unit area which a material is capable of withstanding
without resulting in a permanent deformation of more than a specified amount per unit of gage length after complete
release of load.
PROPORTIONAL LIMIT. The proportional limit of a material is the load per unit area beyond which the increases in
strain cease to be directly proportional to the increases in stress.
PYROMETER. An instrument for measuring temperature.
QUENCHING. Rapid cooling by immersion in liquids or gases.
QUENCHING MEDIA . Quenching media are liquids or gases in which metals are cooled by immersion. Some of the
more common are brine (10 percent sodium chloride solution), water 180C (650F),fish oil, paraffin base petroleum oil,
machine oil, air, engine oil, and commercial quenching oil.
RECALESCENCE. When steel is slowly cooled from a point above the critical temperature, the cooling proceeds at a
uniform rate until the piece reaches a point between 677°and 7040C (1,2500 and 1,3000°F). At this time, the cooling is
noticeably arrested and the metal actually rises in temperature as the change of state again takes place. This change is
the opposite of decalescence and is termed recalescence.
REDUCTION OF AREA. The difference between the original cross-sectional area and that of the smallest area at the
point of rupture. It is usually stated as a percentage of the original area; also called "contraction of area."
REFINING TEMPERATURE OR HEAT. A temperature employed in case hardening to refine the case and core.
The first quench is from a high temperature to refine the core and the second quench is from a lower temperature to
further refine and harden the case.
SCALE. A coating of metallic oxide that forms on heated metal.
SENSITIZING. Developing a condition in stainless steels, which is susceptible to intergranular corrosion. The condition
is usually formed by heating the steel above 8000F and cooling slowly, e.g., welding.
SHEETS COLD ROLLED. The flat products resulting from cold rolling of sheets previously produced by hot rolling.
SHEETS HOT ROLLED. The flat-rolled products resulting from reducing sheet bars on a sheet mill, or slabs, blooms,
and billets on a continuous stripsheet mill.
SOAKING. Holding steel at an elevated temperature for the attainment of uniform temperature throughout the piece.
SOLIDIFICATION RANGE . The temperature range through which metal freezes or solidifies.
SPALLING. The cracking and flaking of small particles of metal from the surface.
SPHEROIDAL OR SPHEROIDIZED CEMETITE. The globular condition of iron carbide resulting from a spheroidizing
treatment. The initial structure may be either pearlitic or martensitic.
1-7
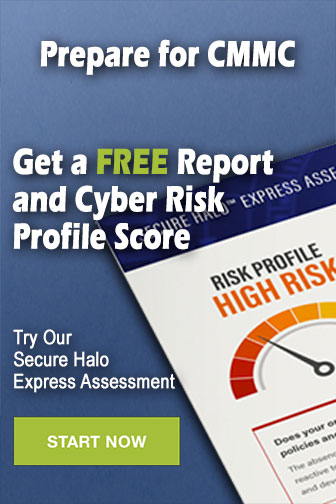