T.O. 1-1A-9
2-5. Steel containing carbon in percentages ranging from 0.30 to 0.50 percent is classed as medium carbon steel. This
steel is especially adaptable for machining, forging, and where surface hardness is important. Certain rod ends, light
forgings, and parts such as Woodruff keys, are made from SAE 1035 steel.
2-6. Steel containing carbon in percentage ranging from 0.50 to 1.05 percent is classed as high carbon steel. The
addition of other elements in varying quantities adds to the hardness of this steel. In the fully heat treated condition it is
very hard and will withstand high shear and wear, but little deformation. It has limited use in aircraft construction. SAE
1095 in sheet form is used for making flat springs and in wire form for making coil springs.
2-7. NICKEL STEELS. The various nickel steels are produced by combining nickel with carbon steel. Some benefits
derived from the use of nickel as an alloy in steel are as follows:
a.
Lowers the percentage of carbon that is necessary for hardening. The lowering of the carbon content makes the
steel more ductile and less susceptible to uneven stress.
b.
Lowers the critical temperature ranges (heating and cooling) and permits the use of lower heating temperatures
for hardening.
c.
Hardening of the nickel alloy steels at moderate rates of cooling has the advantage of lowering the temperature
gradients, reducing internal stress/warpage and permits deeper/more uniform hardening.
d.
The low heat treating temperatures required, reduces the danger of overheating, excessive grain growth and the
consequent development of brittleness.
e.
The characteristics depth hardening from the addition of nickel to steel as an alloy results in good mechanical
properties after quenching and tempering. At a given strength (except for very thin sections/parts) the nickel steels
provide greatly improved elastic properties, impact resistance and toughness.
2-8. CHROMIUM STEELS. Chromium steel is high in hardness, strength, and corrosion resistant properties. SAE
51335 steel is particularly adaptable for heat-treated forgins which require greater toughness and strength than may be
obtained in plain carbon steel.
It may be used for such articles as the balls and rollers of anti-friction bearings.
2-9. CHROMIUM-NICKEL STEELS. Chromium and nickel in various proportions mixed with steel form the chrome-
nickel steels. The general proportion is about two and one-half times as much nickel as chromium. For all ordinary
steels in this group the chromium content ranges from 0.45 to 1.25 percent, while the nickel content ranges from 1 to
2percent. Both nickel and chromium influence the properties of steel; nickel toughens it, while chromium hardens it.
Chrom-nickel steel is used for machined and forged parts requiring strength, ductility toughness and shock resistance.
Parts such as crankshafts and connecting rods are made of SAE 3140 steel.
2-10. Chrome-nickel steel containing approximately 18 percent chromium and 8 percent nickel is known as corrosion-
resistant steel. It is usually identified as aisi types 301, 302, 303, 304, 304L, 309, 316, 316L, 321, 347, 347F or Se, etc.,
however; the basic 18-8 chrome-nickel steel is type 302. The other grades/types have been modified by changing or
adding alloying elements to that contained in the basic alloy. The alloys are varied to obtain the required mechanical
properties for some specific purpose such as improving corrosion resistance or forming machining, welding
characteristics, etc. The following are examples of variations:
a.
301-Chromium and Nickel (approx. 0.5 Nickel) is lowered to increase response to cold working.
b.
302-Basic Type 18 Chromium 8Nickel.
c.
303-8ulfur(s) or Selenium (se) added for improved machining characteristics.
d.
304-Carbon(c) lowered to reduce susceptibility to carbide precipitation. This alloy is still subject to carbide
precipitation from exposure to temperatures 800-1500F range and this shall be considered when it selected for a specific
application.
2-2
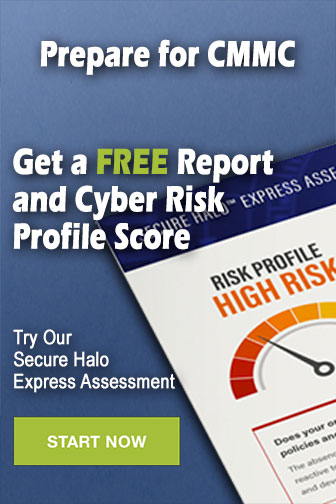