T.O. 1-1A-9
Such crayons are commercially available for a wide range of temperatures under the trade name of "Tempilstiks." The
above method may be used where exact properties after tempering is not too important such as for blacksmith work.
The most desirable method for general aeronautical use, is to determine temperatures by hardness checks, and
subsequent adjustments made as necessary to obtain the properties required. For recommended tempering
temperatures see heat treat data for material/composition involved.
2-28. Steel is usually subjected to the annealing process for the following purposes:
a.
To increase its ductility by reducing hardness and brittleness.
b.
To refine the crystalline structure and remove stresses. Steel which has been cold-worked is usually annealed so
as to increase its ductility. However, a large amount of cold-drawn wire is used in its cold-worked state when very high
yield point and tensile strength are desired and relatively low ductility, is permissible, as in spring wire, piano wire, and
wires for rope and cable. Heating to low temperatures, as in soldering, will destroy these properties. However, rapid
heating will narrow the affected area.
c.
To soften the material so that machining, forming, etc., can be performed.
2-29. NORMALIZING.
Although involving a slightly different heat treatment, normalizing may be classed as a form of annealing. This process
also removes stresses due to machining, forging, bending, and welding. Normalizing may be accomplished in furnaces
used for annealing. The articles are put in the furnace and heated to a point approximately 150 to 225F above the
critical temperature of the steel. After the parts have been held at this temperature for a sufficient time for the parts to be
heated uniformly throughout, they must be removed from the furnace and cooled in still air. Prolonged soaking of the
metal at high temperatures must be avoided, as this practice will cause the grain structure to enlarge. The length of time
required for the soaking temperature will depend upon the mass of metal being treated. The optimum soaking time is
roughly one-quarter hour per inch of diameter or thickness.
2-30. CASE HARDENING.
In many instances it is desirable to produce a hard, wear-resistant surface or "case' over a strong, tough core.
Treatment of this kind is known as "case hardening". This treatment may be accomplished in several ways, the principal
ways being carburizing, cyaniding, and nitriding.
2-31. Flame Hardening/Softening. Surface hardening/softening by applying intense heat (such as that produced by an
Oxy-Acetylene flame) can be accomplished on almost any of the medium carbon or alloys steel, i.e. 1040, 1045, 1137,
1140 etc. The parts are surface hardened, by applying a reducing flame (An Oxidizing flame should never be used} at
such a rate, that the surface is rapidly heated to the proper quenching temperature for the steel being treated. Following
the application of the heat, the part is quenched by a spraying of water/oil rapidly. The fast quench hardens the steel to
the depth that the hardening temperature has penetrated below the surface. The actual hardness resulting will depend
on the rate of cooling from the quenching temperature. In hardening by this method the shape and size/mass of the part
must be considered. Most operations will require special adapted spray nozzles to apply the quenching media, which is
usually water. Normally, flame hardening will produce surface hardness higher than can be obtained by routine furnace
heating and quenching, because surface can be cooled at a faster rate.. If a combination of high strength core and
surface is required some of the medium carbon alloy steels can be heat treated and subsequently surface hardened by
the flame method.
NOTE
This method is not adapted for surface hardening of parts for use in critical applications.
2-32. Surface softening is accomplished by heating the surface to just below the temperature required for hardening and
allowing the material to cool (in air) naturally. This method is sometimes used to soften material that has been hardened
by flame cutting. Often it is necessary to apply the heat in short intervals to prevent exceeding the hardening
temperature.
2-6
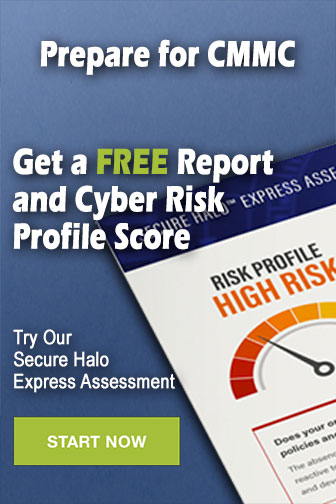