T.O. 1-1A-9
2-52. For all surveys, the furnace or bath temperature shall be allowed to stabilize at the potential test temperature. The
initial survey shall be made at the highest and lowest temperatures of the furnace specified operating range. Periodic
surveys may be made at a convenient temperature within the operating range. The temperature of all test
locations/thermocouples shall be recorded at 5 minute intervals, starting immediately after insertion of the test
thermocouples in the furnace or bath. Reading shall be continued for 1/2-hour or more after furnace control
thermocouple reads within 25 F of original setting. After all the test thermocouples have reached the minimum of the
heat treating range, their maximum variation shall not exceed 25 F (14 C) and shall be within the specified heat
treating temperature range in accordance with Specification MILH-6875 or Table 2-3. If the test indicates that conditions
are not satisfactory, the required chitpges shall be made in the furnace and arrangements of the charge. The furnace
control couples shall be corrected for any deviation from the standard electromative force (EMF) temperature chart as
determined in calibration of the couples.
2-53. FURNACE CONTROL INSTRUMENTS ACCURACY.
2-54. The accuracy of temperature measuring, recording and controlling instruments shall be checked at regular
intervals, not exceeding 3 months or upon request of personnel in charge or authorized (Government) inspector or
representatives. The accuracy of the instrument shall be made by comparison tests with a standardized precision
potentiometer type instrument of known (tested) accuracy used with a calibrated thermocouple. The test thermocouple
shall be located approximately 3 inches from the installed furnace thermocouple(s). The temperature for check shall be
at working temperature with a production load. If instruments are replaced or not used for 3 months they shall be
checked before use.
2-55. SALT BATH CONTROL.
2-56. The bath composition shall be adjusted as frequently as necessary to prevent objectionable attachment of the steel
or alloy to be treated and to permit attainment of the desired mechanical properties of the finished product. The bath will
be checked at least once a month.
2-57. Temperature recording should be of the automatic controlling and recording type, preferably the potentiometer
type. Thermocouples should be placed in a suitable protecting tube, unless the furnace atmosphere is such that undue
deterioration of the thermocouples will not result.
2-58. QUENCHING TANKS AND LIQUIDS. Suitable tanks must be provided for quenching baths. The size of tanks
should be sufficiently large to allow the liquids to remain approximately at room temperature. Circulating pumps and
coolers may be used for maintaining approximately constant temperatures where a large amount of quenching is done.
The location of these tanks is very important due to the fact that insufficiently rapid transfer from the furnace to the
quenching medium may destroy the effects of the heat treatment in many instances.
2-59. The quenching liquids commonly used are as follows: Water at 18C (65F), Commercial Quenching Oil, and Fish
Oil.
2-60. HEAT TREATING PROCEDURES.
2-61. INITIAL FURNACE TEMPERATURES. In normalizing, annealing and hardening where parts are not preheated,
the temperature in that zone of the furnace where works is introduced should be at least 149C (300F) below the
working temperature at the time of insertion of parts of simple design. For parts of complicated design involving abrupt
change of section or sharp corners, the temperature should be at least 260C (500F) below the working temperature.
The furnace must be brought to the proper temperature gradually.
2-11
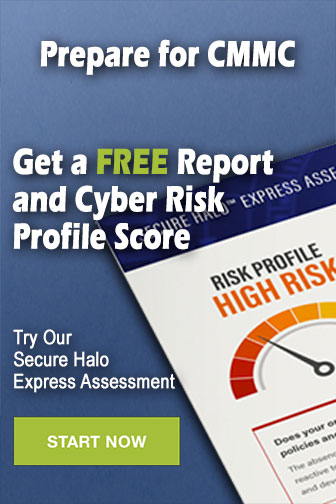