T.O. 1-1A-9
2-68. HARDNESS TESTING.
2-69. GENERAL. Hardness testing is an important factor in the determination of the results of the heat treatment as well
as the condition of the metal before heat treatment and must, therefore, be carefully considered in connection with this
work. The methods of hardness testing in general use are: the Brinell, Rockwell, Vickers, and Shore Scleroscope. Each
of these methods is discussed in section VIII.
2-70. TENSILE STRENGTH. Tempering temperatures listed with the individual steels in Table 2-3 are offered as a
guide for obtaining desired tensile and yield strength of the entire cross section. When the physical properties are
specified in terms of tensile strength, but tension tests are impractical, hardness tests may be employed using the
equivalent hardness values specified in Table 8-3.
2-71. HARDNESS-TENSILE STRENGTH RELATIONSHIP. The approximate relationship between the tensile strength
and hardness is indicated in Table 8-3. This table is to be used as a guide. It applied only to the plain carbon and low
alloy steels not to corrosion-resistant, magnet, valve, or tool steels. When a narrow range of hardness is required, the
tests to determine the relationship between hardness and strength should be made on the actual part. Hardness values
should be within a range of two points Rockwell or 20 points Brinell or Vickers. The tensile strength hardness relationship
is quite uniform for parts which are sufficiently large and rigid to permit obtaining a full depression on a flat surface
without deflection of the piece. For cylindrical parts of less than 1 inch in diameter, the Rockwell reading will be lower
than indicated in the table for the corresponding tensile strength. Any process which affects the surface, such as buffing
and plating, or the presence of decarburized or porous areas and hard spots, will affect the corresponding relation
between hardness and tensile strength. Therefore, these surfaces must be adequately removed by grinding before
measurements are made.
2-72. In making hardness measurements on tubular sections, correction factors must be determined and applied to the
observed readings in order to compensate for the roundness and deflection of the tubing under the pressure of the
penetrator. This may be impractical because every tube size and wall thickness would have a different factor. As an
alternate, the following procedure may be used: Short lengths may be cut from the tube. A mandrel long enough to
extend out both ends of the tube and slightly smaller in diameter than the inner diameter of the tube is then passed
through the section and the ends supported in "V" supports on the hardness tester. Hardness readings may then be
taken on the tubing.
2-73. SPECIFICATION CROSS REFERENCE.
Table 2-2 is a cross reference index listing the steel and alloy types and the corresponding Federal, Military, and
aeronautical material specifications for the different configurations. Where two or more specifications cover the same
material, stock material meeting the requirements of a military specification shall be used for all aeronautical structural
items. Some of the specifications listed in Table 2-2 are for reference only, and are not approved for Air Force use.
2-13
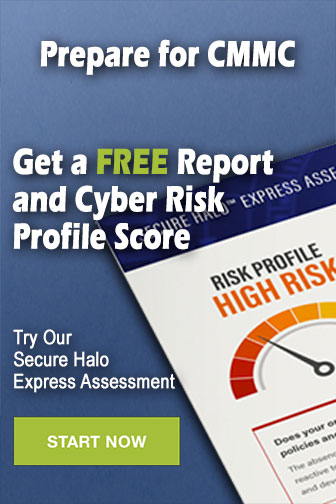