T.O. 1-1A-9
2-40. Carburized steel parts are rarely used without subsequent heat treatment, which consists of several steps to obtain
optimum hardness in the case, and optimum strength and ductility in the core. Grain size of the core and case is refined.
a.
Refining the core is accomplished by reheating the parts to a point just above the critical temperature of the
steel. After soaking for a sufficient time to insure uniform heating, the parts are quenched in oil.
b.
The hardening temperature for the high carbon case is well below that of the core. It is, therefore, necessary to
heat the parts again to the critical temperature of the case and quench them in oil to produce the required hardness. A
soaking period of 10 minutes is generally sufficient.
c.
A final stress relieving operation is necessary to minimize the hardening stresses produced by the previous
treatment. The stress relieving temperature is generally around 350 F. This is accomplished by heating, soaking until
uniformly heated, and cooling in still air. When extreme hardness is desired, the temperature should be carefully held to
the lower limit of the range.
2-41. CYANIDING. Steel parts may be surface-hardened by heating while in contact with a cyanid salt, followed by
quenching. Only a thin case is obtained by this method and it is, therefore, seldom used in connection with aircraft
construction or repair. Cyaniding is, however, a rapid and economical method of case hardening, and may be used in
some instances for relatively unimportant parts. The work to be hardened is immersed in a bath of molten sodium or
potassium cyanide from 30 to 60 minutes. The cyanide bath should be mainlined at temperature to 760 C to 899 C
(1,400 F to 1,650 F). Immediately after removal from the bath, the parts are quenched in water. The case obtained in
this manner is due principally to the formation of carbides and nitrides on the surface of the steel. The use of a closed
pot and ventilating hood are required for cyaniding, as cyanide vapors are extremely poisonous.
2-42. NITRIDING. This method of case hardening is advantageous due to the fact that a harder case is obtained than
by carburizing. Many engine parts such as cylinder barrels and gears may be treated in this way. Nitriding is generally
applied to certain special steel alloys, one of the essential constituents of which is aluminum. The process involves the
exposing of the parts to ammonia gas or other nitrogenous materials for 20 to 100 hours at 950F. The container in
which the work and Ammonia gas are brought in contact must be airtight and capable of maintaining good circulation and
even temperature throughout. The depth of case obtained by nitriding is about 0.015 inch if heated for 50 hours. The
nitriding process does not affect the physical state of the core if the preceding tempering temperature was 950 F or
over.
When a part is to be only partially treated, tinning of any surface will prevent it from being nitrides. Nitrided surfaces can
be reheated to 950 F with out losing any of their hardness. However, if heated above that temperature, the hardness is
rapidly lost and cannot be regained by retreatment. Prior to any nitriding treatment, all decarburized metal must be
removed to prevent flaking of the nitrided case. When no distortion is permissible in the nitrided part, it is necessary to
normalize the steel prior to nitriding to remove all strains resulting from the forging, quenching, or machining.
2-43. HEAT TREATING EQUIPMENT.
Equipment necessary for heat treating consists of a suitable means for bringing the metal to the required temperature
measuring and controlling device, and quenching medium. Heat may, in some instances, be supplied by means of a
forge or welding torch; however, for the treatment required in aircraft work, a furnace is necessary. Various jigs and
fixtures are sometimes needed for controlling quenching and preventing warping.
2-44. FURNACES. Heat treating furnaces are of many designs and no one size or type perfectly fills every heat treating
requirement. The size and quantity of metal to be treated and the various treatments required determine the size and
type of furnace most suitable for each individual case. The furnace should be of a suitable type and design for the
purpose intended and should be capable of maintaining within the working zone a temperature varying not more than +
or 14 C ( 25F) for the desired value.
2-8
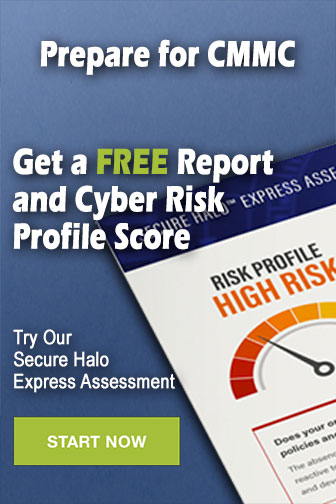