T.O. 1-1A-9
c.
An article should be quenched in such a manner that all parts will be cooled uniformly and with the least possible
distortion. For example, a gear wheel or shaft should be quenched in a vertical position.
d.
Irregularly shaped sections should be immersed in such a manner that the parts of the greatest section thickness
enters the bath first.
2-20. QUENCHING MEDIUM.
2-21. Oil is much slower in action than water, and the tendency of heated steel to warp or crack when quenched may be
greatly reduced by its use. Unfortunately, parts made from high carbon steel will not develop maximum hardness when
quenched in oil unless they are quite thin in cross section. In aircraft, however, it is generally used and is recommended
in all cases where it will produce the desired degree of hardness.
NOTE
Alloy steels should never be quenched in water.
2-22. In certain cases water is used in the quenching of steel for the hardening process. The water bath should be
approximately 18 C (65F), as extremely cold water is apt to warp or crack the steel and water above this temperature
will not produce the required hardness.
2-23. A 10% salt brine (sodium chloride) solution is used when higher cooling rates are desired. A 10% salt brine
solution is made by dissolving 0.89 pound of salt per gallon of water.
2-24. For many articles such as milling cutters and similar tools, a bath of water covered by a film of oil is occasionally
used. When the steel is plunged through this oil film a thin coating will adhere to it, retarding the cooling effect of the
water slightly, thus reducing the tendency to crack due to contraction.
2-25. STRAIGHTENING OF PARTSWARPED IN QUENCHING. Warped parts must be straightened by first heating to
below the tempering temperature of the article, and then applying pressure. This pressure should be continued until the
piece is cooled. It is desirable to retemper the part after straightening at the straightening temperature. No attempt
should be made to straighten hardened steel without heating, regardless of the number of times it has been previously
heated, as steel in its hardened condition cannot be bent or sprung cold with any degree of safety.
2-26. TEMPERING (DRAWING).
Steel that has been hardened by rapid cooling from a point slightly above its critical range is often harder than necessary
and generally too brittle for most purposes. In addition, it is under severe internal stress. In order to relieve the stresses
and reduce the brittleness or restore ductility the metal is always "tempered". Tempering consists in reheating the steel
to a temperature below the critical range (usually in the neighborhood of 600 1200F). This reheating causes a
coalescence and enlargement of the fine carbide particles produced by drastic quenching, and thus tends to soften the
steel. The desired strength wanted will determine the tempering temperature. This is accomplished in the same types of
furnaces as are used for hardening and annealing. Less refined methods are sometimes used for tempering small tools.
2-27. As in the case of hardening, tempering temperatures may be approximately determined by color. These colors
appear only on the surface and are due to a thin film of oxide which forms on the metal after the temperature reaches
232 C (450 F). In order to see the tempering colors, the surface must be brightened. A buff stick consisting of a piece
of wood with emery cloth attached is ordinarily used for this purpose. When tempering by the color method, an open
flame of heated iron plate is ordinarily used as the heating medium. Although the color method is convenient, it should
not be used unless adequate facilities for determining temperature are not obtainable. Tempering temperatures can also
be determined by the use of crayons of known melting point.
2-5
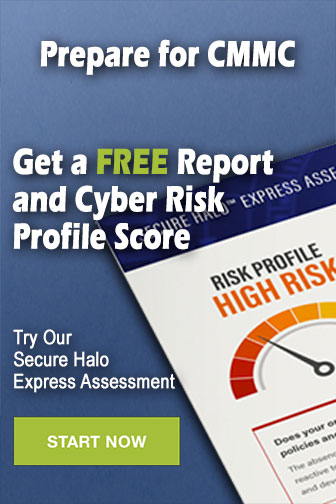