T.O. 1-1A-9
2-33. Induction Hardening/Heating. The induction method of heating can be used to surface harden steels, in a manner
similar to that used for flame hardening. The exception is that the heat for hardening is produced by placing the part in a
magnetic field (electrical) specifically designed for the purpose. Parts hardened (surface) by this method will be limited
to capability and size of loop/coil used to produce the magnetic field.
2-34. In some instances the induction method can be used to deep harden; the extent will depend on exposure/dwell
time, intensity of the magnetic field, and the size of the part to be treated.
2-35. CARBURIZING. At elevated temperatures iron can react with gaseous carbon compounds to form iron carbide.
By heating steel, while in contact with a carbon-aceous substance, carbonic gases given off by this material will penetrate
the steel to an amount proportional to the time and temperature. For example, if mild or soft steel is heated to 732C
(1,350 F) in an atmosphere of carbonic gases, it will absorb carbon from the gas until a carbon content of approximately
0.80 percent has been attained at the surface, this being the saturation point of the steel for the particular temperature.
By increasing the heat to 899° C (1,650 F), the same steel will absorb carbon from the gas until a carbon content of
approximately 1.1 percent has been attained, which is the saturation point for the increased temperature.
2-36. The carburizing process may be applied to both plain carbon and alloy steels provided they are within the low
carbon range. Specifically, the carburizing steels are those containing not more than 0.20 percent carbon. The lower the
carbon content in the steel, the more readily it will absorb carbon during the carburizing process.
2-37. The amount of carbon absorbed and the thickness of the case obtained increases with time; however; the
carburization progresses more slowly as the carbon content increases during the process. The length of time required to
produce the desired degree of carburization material used and the temperature to which the metal is subjected. It is
apparent that, in carburizing, carbon travels slowly from the outside toward the inside center, and therefore, the
proportion of carbon absorbed must decrease from the outside to the inside.
2-38. Solid, liquid, and gas carburizing methods are employed:
a.
The simplest method of carburizing consists of soaking the parts at an elevated temperature while in contact with
solid carbonaceous material such as wood charcoal, bone charcoal and charred leather.
b.
Liquid carburizing consists of immersing the parts in a liquid salt bath, heated to the proper temperature. The
carbon penetrates the steel as in the solid method producing the desired case.
c.
Gas carburizing consists of heating the parts in a retort and subjecting them to a carbonaceous gas such as
carbon monoxide or the common fuel gases. This process is particularly adaptable to certain engine parts.
2-39. When pack carburizing, the parts are packed with the carburizing material in a sealed steel container to prevent
the solid carburizing compound from burning and to retain the carbon monoxide and dioxide gases. Nichrome boxes,
capped pipes of mild steel, or welded mild steel boxes may be used. Nichrome boxes are most economical for
production because they withstand oxidation. Capped pipes of mild steel or welded mild steel boxes are useful only as
substitutes. The container should be so placed as to allow the heat to circulate entirely around it. The furnace must be
brought to the carburizing temperature as quickly as possible and held at this heat from 1 to 16 hours, depending upon
the depth of case desired and the size of the work. After carburizing, the container should be removed and allowed to
cool in air or the parts removed from the carburizing compound and quenched in oil or water. The air cooling, although
slow, reduces warpage and is advisable in many cases.
2-7
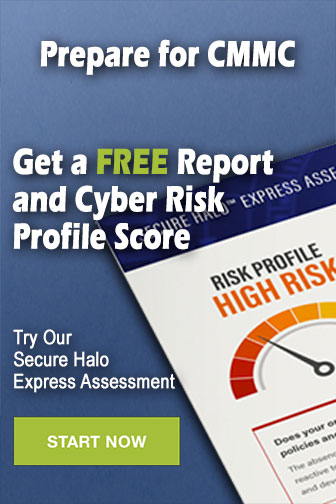