T.O. 1-1A-9
EXPOSURE. Heating to or subjecting to an elevating temperature or environment for a certain period of time.
ETCHING. Attack of metals structure by reagents. In metallography, the process of revealing structural details by the
preferential attack of reagents on a metal surface.
a. Micro-etching is for the examination of the sample under a microscope and for this purpose the sample must be
very carefully polished (by an experienced person) prior to etching.
b.
Macro-etching is for the examination of the sample under a low power magnifying glass or by unaided eye.
High polishing for this purpose is not absolutely essential; however, a good polish is necessary.
c. Deep-etching is a form of macro-etching in which the sample with regular cut surface may be immersed in hot
hydrochloric acid (50% acqueous solution) and then examined for major defects such as inclusions, segregations, cracks,
etc.
FATIGUE. The phenomenon of the progressive fracture of a metal by means of a crack which spreads under repeated
cycles of stress.
FATIGUE LIMIT. Usually used as synonymous with endurance limit.
FERRITE. A solution in which alpha iron is the solvent, and which is characterized by a body centered cubic crystal
structure.
FILLET. A concave junction of two surfaces usually perpendicular.
FLAME HARDENING. A process of hardening a ferrous alloy by heating it above the transformation range by means of
a high-temperature flame and then cooling as required.
FORGING STRAINS. Elastic strains resulting from forging or from cooling from the temperature.
FORMING. To shape or fashion with hand/tools or by a shape or mold.
FRACTURE TESTING. A test used to determine type of structure, carbon content and the presence of internal defects.
The test specimen is broken by any method that will produce a clean sharp fracture. The fracture is then examined by
eye or with the aid of a low former magnifying glass. A trained/experienced observer will determine grain size;
approximate depth of carburized or decarburized surface area; the presence of inclusions of dirty steel; and defects such
as seams, cracks, pipes bursts and flakes.
FULLY HARDENED. Applies generally to the maximum hardness obtainable. (In particular, applies to materials that are
hardened by a strain and/or age hardening process).
FUSIBLE ALLOYS. A group of nonferrous alloys which melt at relatively low temperatures. They usually consist of
bismuth, lead, tin, etc., in various proportions, and iron only as an impurity.
GALVANIC SERIES. A list of metals and alloys arranged in order of their relative potentials in a given environment.
The galvanic series indicates the tendency of the several metals and alloys to set up galvanic corrosion. The relative
position within a group sometimes changes with external conditions, but it is only rarely that changes occur from group to
group.
GRAINS. Individual crystals in metal. When metal is in molten state, the atoms have no uniform grouping. However,
upon solidification they arrange themselves in a geometric pattern.
GRAIN GROWTH. An increase in the grain size of metal.
HARDENABILITY. The ability of an alloy to harden fully throughout the entire section thickness either by cold working or
heat treatment. The maximum thickness at which this may be accomplished can be used as a measure of hardenability.
HARDENING. Hardening is accomplished by heating the metal to a specified temperature, then rapidly cooling by
quenching in oil, water, or brine. This treatment produces a fine grain structure, extreme hardness, maximum tensile
strength, and minimum ductility.
HARDNESS. Hardness refers to the ability of a material to resist abrasion, penetration, indentation, or cutting action.
The wearing qualities of a material are in part dependent upon its hardness. Hardness and strength are properties which
are closely related for wrought alloys.
HARDNESS TESTING. Test used to determine the ability of a metal to resist penetration. The test results are usually
directly related to tensile and yield strength of the metal involved. An exception would be case hardness. See Section
VI for typical testing methods.
HEAT TINTING. Heating a specimen with a suitable surface in air for the purpose of developing the structure by
oxidizing or otherwise affecting the different constituents.
1-5
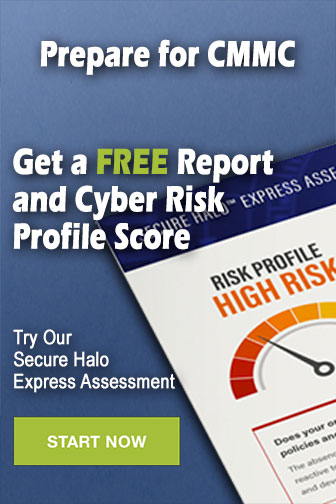