T.O. 1-1A-9
e. Weld joints shall be protected while at high temperature by use of flux such as Spec bML-F-7516 and by shield
of properly adjusted (neutral as possible) welding flame. The flux protection shall be applied (sparingly) on all surfaces
that may reach oxidizing temperatures (8000-15000F). The flux is applied by brushing on parts to be welded and by
dipping end of filler rod. The flux is applied underneath the weld as well as on top and heat zone is kept covered for
sufficient time to prevent oxidizing attack. When working with tacked assemblies, flux is applied before tacking, cleaned
and complete area as cited above is fluxed before final welding. In no case shall parts be welded by the gas process
without the use of flux of proper grade.
f. When possible, welding should be accomplished using carefully designed jigs. The jigs should be designed and
arranged to serve dual purpose of absorbing excess heat and holding assembly in accurate alignment. When it is
necessary to align parts by tacking, the tacks should be closely spaced approximately every 2" or closer. The tacks
should be small enough to permit re-fusion into final weld. If buckling is encountered during the tacking operation, the
part should be reshaped to specified dimensions before preceding with welding operation. Prior to completing the
welding operation, the tacks should be cleaned and prospective seam/heat affected area refluxed.
NOTE
For additional information see Spec MIL-W-8611, MIL-E-8697, MIL-R-5031, MIL-R-5632, MIL-E-
6843, MIL-E-6844, MIL-E-22200, and MIL-HDBK-5.
2-186. SPOT/SEAM WELDING - GENERAL.
2-187. Spot/seam welding is a resistance welding process where two or more sheets of metal are clamped between two
electrodes (copper/copper alloy) and a current is passed through the pieces to weld them together. The contact area of
the electrode with the work pieces is the location of maximum temperature and therefore the weld is confined to a
relatively small area (spot/seam).
2-188. Factors requiring consideration when spot/seam welding the corrosion resisting steels and iron alloys:
a. The corrosion resistant properties of the various alloys are sensitive to heat. The temperatures used and time
at temperature must be accurately controlled to minimize adverse effect of heat and at the same time sufficient heat and
pressure must be applied to attain required physical properties.
b. The amperage or duration of current flow (dwell time) should be decreased in comparison to those used for
carbon steel.
c. The high room and elevated temperature strengths makes it necessary to employ higher pressure than used for
other materials i.e., aluminum, lower carbon steels, etc.
d. Due to the higher co-efficient of expansion of the chromium-nickel grades, allowances must be made in setting
up for welding and in welding sequence. The extent will depend upon the amount of heat generated in the specific
assembly' and assemblies involved.
e. Some types of the corrosion resistant materials are chromium nickel steels (300 series).
2-189. The requirements for spot welding of non-hardening steels (by the welding process) austenitic steel, nickel alloys,
and heat-resisting alloys for use on various weapons and components are cited in MIL-W-6858 (Group b). Welds in
accordance with this specification are classified as follows:
a. Class A Used in joints, the single failure of which during any operating condition would cause loss of the
weapons system or one of its major components, loss of control, unintentional release of, or inability to release any
armament store, failure of gun installation components or which may cause significant injury to occupants of the manned
weapons system.
b. Class B Used in joints, the failure of which would reduce the overall strength of the weapon system or preclude
the intended functioning or use of equipment.
c. Class C - A weld which is considered non-critical and for which no stress analysis is requested/required.
2-190. EQUIPMENT FOR SPOT WELDING. The welding machine shall consists of a suitable source of electrical
energy, electrodes and means of adequately cooling electrodes and a means of reliably controlling and indicating the
magnitude of the current welding force/ pressure and time of current flow. The current and force controls shall operate
so that no current flows until the welding force is applied at the welding electrodes. The current (welding) shall be cut off
before the force is removed.
2-191. The welding machines shall be qualified to meet the weld requirements for the highest classification, i.e., Class A,
B or C for which it is to be used in production. A machine qualified for a higher classification is automatically qualified for
a lower weld classification.
2-192. The welding machines shall be requalified if machine is rebuilt or if significant operational changes are made. A
change of location within a shop, not involving a change in power line, does not necessitate requalification.
2-93
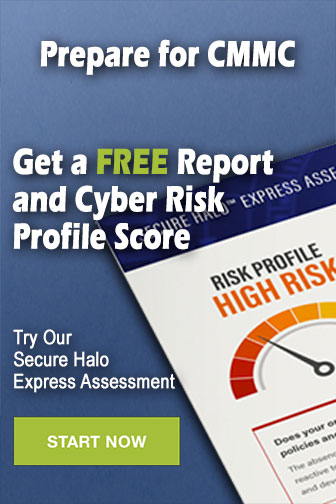