T.O. 1-1A-9
TABLE 2-18. FUSION WELDING CHARACTERISTICS OF CORROSION RESISTING STEEL - GENERAL(CONTD)
ALLOY/DESIGN
RECOMMENDED
FILLER MATERIAL/SPEC
HEAT TREATMENT
REMARKS
TYPE
STRUCTURE
TYPE
ELECTRODE
ROD
PREHEAT
POSTHEAT
MATERIAL
TREAT
15-7
The molybdenum add-
MO Cont'd
tive in this alloy
causes larger amounts
of delta ferrite or
free ferrite to form
in the weld deposit
upon solidification.
The amount of
ferrite requires some
control in order to
maintain good ductility
in the highest strength
conditions. This con-
trol can be accom-
plished by the use of
filler metal of appro-
priate chemical com-
position, through heat
treatment or both.
17-
Martensitic
17-4PH
AMS 5825
Not re-
Heat treat or
Readily weldable using
4PH
This alloy
AMS 5827
quired.
anneal.
arc and resistance
is Austeni-
welding processes
itc at elevat-
commonly used with
ed tempera-
Austenitic stainless
ture but
steels. Sound welds
transforms
with properties com-
to Marton-
parable to parent
sitic upon
metal can be obtained
cooling.
using weld metal of
same composition and
post weld annealing or
heat treating. Spot
welding and seam
welding readily ac-
complished using pro-
cedures similar to
those used for
austenitic stainless.
Best results obtained
by in partly or fully
heated treated condit-
ions. Resistance butt
welding not currently
recommended.
17-
Austenitic
17-7PH
AMS 5825
Not re-
feat treat or
Fusion welding and
7PH
in cond-
AMS 5827
quired.
anneal. Fusion
spot welding can be
ition A.
17-4PH
welded joints
readily accomplished.
Heat treat-
using 17-4PH
Best results are ob-
ed condit-
electrode can
tained by spot welding
ion are
be heat treated
partial or fully heat
martensi--
to 170 KSI
treated material. The
tic with
ultimate ten-
surface to be welded
some auste-
site by aus-
should be cleaned by
nitic.
tenitic condi-
vapor or sand to avoid
tioning at 1400 porous welds.
Inert
F followed by
gas tungsten are of an-
2-98
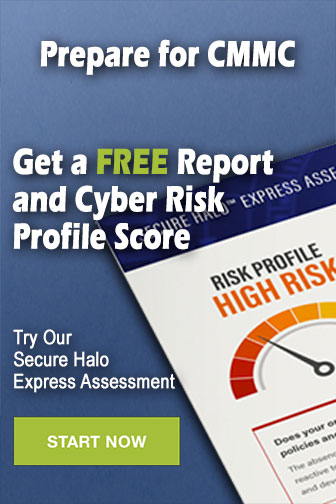