T.O. 1-1A-9
TABLE 2-18. FUSION WELDING CHARACTERISTICS OF CORROSION RESISTING STEEL - GENERAL(CONTD)
ALLOY/DESIGN
RECOMMENDED
FILLER MATERIAL/SPEC
HEAT TREATMENT
REMARKS
TYPE
STRUCTURE
TYPE
ELECTRODE
ROD
PREHEAT
POSTHEAT
MATERIAL
TREAT
321
Austenitic
347
MIL-E-6844
Class 5,
Same as
Postweld
One of best grades for
Class 5,
Class 5A,
above.
anneal not re-
fabrication of parts by
AMS 5681
AMS 5680
quired unless
welding. Not subject
material is
to intergranular cor-
overheated to
rosion unless over
above 1900
F
heated to above 1900
F.
(See Remarks).
Heating at this tem-
perature followed by
rapid cooling & re-
heating at approxi-
mately 800
- 1500°F
will reduce resistance
to intergranular at-
tack due to carbide
precipitation. For
restoration of this
sensitized condition,
material should be
stabilized or fully
annealed.
347
Austenitic
347
MILE-6844
MIL-R-5031
Same as
Post well an-
Primary use is for
348
Austenitic
Class 5
Class 5
above.
neal not re-
fabrication of parts
AMS 5681
Class 5A
quired unless
by welding without
AMS 5680
overheated to
postweld annealing,
above 2150
F
however, it is harder
for prolonged
to fusion weld than
periods, how-
304L. Difficulty may
ever, after
be experienced in
fabrication a
welding heavy sections
stress relief
due to cracking. For
is recommen-
restoration of sen-
ded.
sitized condition,
material should be
stabilized or fully
annealed.
403
Martensitic
309
MIL-E-6844
MII-R-5031
300
F
1350
F
Fusion welding of
410
310
Class 2/3
Class 2/3
followed by
type 403 and 410 can
416
410
AMS 5777
AMS 5776
cooling at rate
be accomplished us-
of 100
F per
ing electrode of same
See Remarks
hour maximum
composition if mater-
to 1100
F is
ial is to be heat treat-
necessary to
ed after welding.
prevent crack-
Type 309/310 ele-
ing. Type 416
ctrodes can be used
should be an-
if material is to be
nealed at 1450° used in a welded con-
F after weld-
dition. 416 is not
ing to improve
generally recommend-
ductility &
ed but can be fusion
corrosion re-
welded to a limited
sistance.
extent. 416 requires
annealing after weld-
ing to improve both
ductility and corros-
ion resistance.
2-96
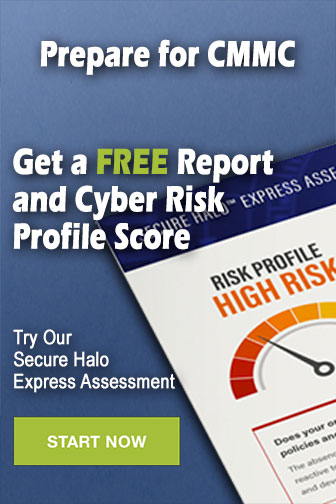