T.O. 1-1A-9
j. Upon completion of welding, pass shut-off current before removing gas shield to avoid oxidation and tinting of
lead.
k. Use appropriate amperage, voltage, electrode and gas flow. For general operating data see Table 2-17.
1. Have periodic tests made to determine if penetration, weld deposits, etc., are being accomplished in
accordance with specified requirements and if changes are required/necessary to correct unsatisfactory condition.
2-183. Edges/joints for use with the inert gas shielded arc method are prepared essentially the same as those used with
other methods except consideration is given to inerting back side of weld to prevent oxidation. In addition, particular
emphasis is necessary to assure that joints are accurate, i.e., gap or butt joint shall be uniform, especially when no filler
metal is used. Joints made without filler metal will generally develop a slight depression down the center line of the weld.
The depression can be controlled to some extent by slightly bending mating edges of metal being welded. The bent
edge provides a little additional metal to the joint. The joint is prepared by bending material 1/16 3/32 inch from each
edge upward approximately 300 (toward welding side) and then butting together before welding. The above will slightly
reduce overall dimensions and allowance for material lost must be made when fabricating precision or close tolerance
parts.
2-184. GAS WELDING OF CORROSION RESISTING STEELS AND NICKEL CHROMIUM IRON ALLOY.
2-185. Typical characteristics/controls associated with gas welding are as follows:
a. Temperature (welding) is lower and less concentrated than the arc methods. Due to this factor the process
should be limited to thickness (0.010" 0.125") that can be rapidly heated to fusion temperature. This is necessary so that
time at heat can be minimized and adverse thermal effects, i.e., harmful carbide precipitation, warpage and grain growth
can be held to a minimum.
b. Welding speeds are slower in comparison to other methods.
c. The tips used for welding should be one or two sizes smaller than those used for welding the low carbon steels
of the same thickness, see Table 2-18. The flame should be slightly reducing with an excess acetylene feather not
exceeding 1/16". The flow should be as near neutral as possible without the possibility of having either an oxidizing or
carbonizing flame, both of which are detrimental to the ductility and corrosion resistance of the metal. A soft flame,
although adjusted to have the appearance of being neutral, is actually oxidizing.
d. Joint designs are of the usual hand, i.e., straight butt, girth and upraised edge/flanged. On thin material, joining
can be accomplished by forming a small flange equal to metal thickness, but not to exceed 1/16", on each edge and
interfused together in lieu of using filler metal. Butt joints can also be used and thickness above 0.040" 0.080" should be
gaped approximately 1/2" thickness of material to insure penetration. Thickness of 0.080 and larger should be prepared
by beveling edges.
TABLE 2-17. RELATION BETWEEN SHEET THICKNESS, CURRENT REQUIRED, WELDING SPEED FILLER ROD
(WHERE REQUIRED) FOR WELDING OF CORROSION RESISTING STEELS AND NICKEL BASE ALLOYS.
THICKNESS OF
ELECTRODE DIA
CURRENT RANGE AMPS
ARGON FLOW/2
WELDING
SHEET
INCH
V/1 DE, STRAIGHT
SPEED INCH
POLARITY AND A. C.
PER MINUTE
0.010
1/32
12-16
3 litres
20-40
0.015
1/32
14-20
3 litres
20-40
0.020
1/32
20-35
3 litres
20-40
0.025
1/32
20-40
3-4 litres
15-40
0.032
1/32
25-40
4 litres
15-40
0.040
1/16
50-130
4 litres
15-40
0.050
1/16
80-165
4 litres
15-40
0.0625
1/16
90-170
4-5 litres
15-40
0.080
3/32
125-200
5 litres
10-35
0.125
1/8
150-275
5 litres
10-30
1/ Welding voltage should be approximately 15.
2/ These figures are based on calibration for oxygen flow.
2-92
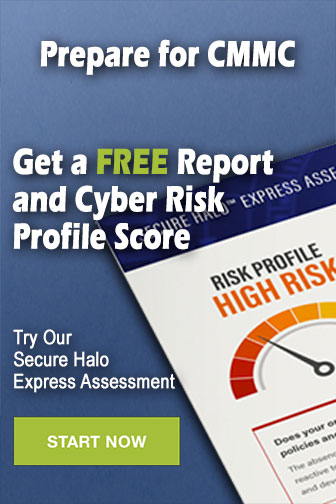