T.O. 1-1A-9
2-152. WELDING OF CORROSION RESISTING STAINLESS STEEL.
Of the 18-8 series only the types with a maximum carbon content of 0.08% and unstabilized (Type 304, 304L, 316L) or
maximum carbon of 0.10%and stabilized with titantium or columbium (Types 321 and 347) in the annealed condition,
have excellent welding qualities. The balance of this series has only fair to poor weldability. Welding of any of the
corrosion resisting steels (Type 301, 302 and other types) in work hardened condition, i.e., 1/4 hard, 1/2 hard, etc., will
only be accomplished as directed by applicable technical order or other approved technical data for the specific
equipment, aircraft or missile involved.
2-153. The 300 series alloys are more susceptible to intergranular carbide precipitation than others. Actual susceptibility
is dependent on carbon content and whether the alloy contains stabilizing elements (columbium or titantium). When the
stabilized grades (321 and 347) are heated to temperatures (8000-15000F) where carbide precipitation occurs, the
stabilizing elements combine preferentially with carbon to form their own carbides tying up the carbon to avoid the
formation of chromium carbide and keeping the chromium in solution. The above is the basis for selecting certain types
as preferred welding grades.
2-154. STRAIGHT CHROME TYPE 400 SERIES. Welding of the straight chrome corrosion resisting steels is normally
limited to hardenable grades 403, 410, 431 and non-hardenable grades 430, 443, and 446. As a group, these grades
have certain characteristics which influence their reaction when subjected to welding temperature. The characteristics
are as follows:
a. Heat conduction rate in comparison to carbon steel is 50% or less. The low heat conduction rate can contribute
to wrapping and the establishment of stress.
b. They are subject to grain growth at temperatures in excess of 1650°F.
c. Tensile strength decreases rapidly with increase in temperature.
2-155. Of the hardenable series, the best grades for welding are those containing 11.50-14.00 chromium with
0.15%mwlTmllmcarbon. To weld these grades preheating and post-heating at a suitable temperature (see Table 2-18)
prior to, during and after welding, to reduce or smooth out the effect of sharp beat gradients, accentuated by low rate of
heat conductivity, is essential. If appropriate steps are not taken, fracture can result from thermal expansion and
volumetric changes. Post-heating, such as annealing expediously upon completion of welding will prevent local
Concentrations of high stress in heat affected zone due to contraction. The necessity for proper thermal treatment of a
hardenable material cannot be over emphasized, especially where heavy thicknesses are involved.
2-156. Post-heating treatment of the hardenable grades can be accomplished by treating as cited in Table 2-18, and by
annealing at 1500°F followed by controlled cooling to 1100IF at a rate of 50 degrees per hour and then air cooling.
2-157. The outstanding characteristics/advantage associated with welding of these grades is that welds made with filler
metal of same composition can be heat-treated, thus allowing utilization of the material in many important structural
applications and other places where high abrasion resistant weld joints are required.
2-158. The non-hardenable grades (430, 442, 446) containing chromium between 16-28% are susceptible to
intergranular corrosion as a result of the temperature used in welding. The reaction of these grades to intergranular
corrosion is opposite of that prevail with the 18-8 grades. These grades are susceptible to intergranular corrosion when
rapidly cooled from temperatures above 17000 F, where the 18-8 grades are susceptible when slowly cooled through the
800°1500F range (as previously stated).
2-159. The heat treatment required to remove precipitation for restoration of corrosion resistance is also different.
Instead of controlled cooling in the furnace, the material is air cooled or quenched in water from the annealing
temperature. The temperatures (2nnp,ling) used to restore mechanical properties to fully soft condition and corrosion
resistance after welding (particularly in case of Types 430 and 442) as follows:
a. Types 430 and 430F - heat to 1200°-1500°F and air cool.
b. Type 442 - heat to 1450°-1550F and air cool or water quench.
c. Type 446 - heat to 1575-1650F and air cool or water quench (preferably water quench).
2-160. NICKEL CHROMIUM IRONALLOYANDNICKEL ALLOYS. Alloys normally encountered to be welded are
MONEL K, Inconel Alloy 600, x 750, Hastalloy "C". and 'K" generally good mechanical properties, strength and ductility
are inherent in welded joints in all nickel and high nickel alloys. In addition thermal or chemical (passivation) treatment is
not usually needed after welding to retain or restore corrosion resistance. However, thermal treatment is required to fulfill
other specified requirements and chemical or abrasive cleaning are utilized to remove scale.
2-161. Similar to the welding of other metals, the weld joint area should be clean. All preservatives, dirt, grease, oil,
scale, paint, crayon marks, etc. shall be removed before starting the welding operation. The nickel and nickel alloys are
susceptible to embrittlement by sulfur and lead which may be contained in the residual contaminants during the welding
process.
2-88
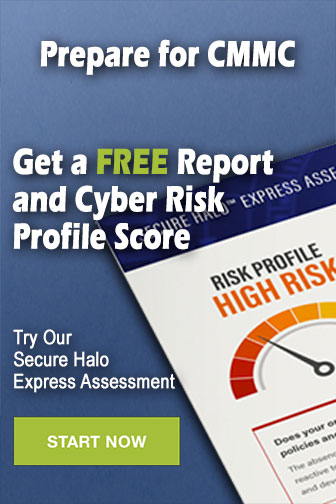