T.O. 1-1
TABLE 2-16. RELATION BETWEEN SHEET THICKNESS, WIRE DIA, CURRENT AND EDGE PREPARATION FOR
METALIC ARC WELDING OF CORROSION RESISTING STEELS.
ELECTRODE
EDGE
THICKNESS
AMPS
WIRE DIA
PREPARATION
OF SHEET
JOINT/GAP
BEADS
APPROX
INCHES
SEE NOTES
0.031
Tight
1
30
1/16-5/65
Square/sheared
0.0375
Tight
1
30-35
5/64-3/32
Square/sheared
0.0438
Tight
1
35-45
5j64-3/32
Square/sheared
0.050
Tight
1
35-50
3/32
Square/sheared
0.062
Tight
1
35-55
3/32
Square/sheared
0.080
1/2T" (040)
1
60-100
3/32-1/8
Square/sheared
0.093
1/16"
1
130
5/32
Sheared
or 2 from both
sides (1st
in V) 2nd
130
5/32
Single V Bevel
100
other sides
100
1/8
30 on a side
with 1/16
throat
0.187 (3/16")
1/16"
2
1st in V
130
5/32
2nd other side
110
1/8
Bevel 30 on a
side 1/16"
throat
0.250 1/4"
1/16"
2
1st in V
170
3/16
Single V
2nd other side
130
Bevel 30 on a
side 1/16"
throat
NOTE: The edges should be cut straight and when setting up for welding they should be in tight contact
or with a uniform gap throughout the length of weld joint.
2-173. For welding thin material less than 1/8"jigging using copper chill bar for backing and steel hold down block bar are
preferred to tacking, if practical. The use of chill block affords better control over the adverse effects of heat, i.e.,
warping and loss of corrosion resistance due to carbide precipitation. In sheet thickness, (up to 0.125") better results are
usually obtained by welding from one side in a jig than are obtained by tacked assemblies welded the same way.
2-174. As with types welding material shall be clean before attempting to weld.
2-175. TREATMENT OF WELD ZONES AFTER WELDING. Recommended procedures for treatment of weld zones
after welding has been completed are as follows:
1. All flux shall be removed after welding in the interest of obtaining maximum corrosion resistance. Flux
remaining on the material can become molten and cause slagging attack and scaling when subjected to high temperature
applications. Flux can be removed by striking with a sharp hammer, vigorous brushing with a stainless wire brush and
abrasive blasting followed by passivation (acid treatment) for final removal of any residue including scale.
2. Weld spatters shall be completely removed. If the spatter remains in place (on the metal) it is a source for
corrosion attack under normal service conditions. Such attack is usually crevice corrosion around edges or pitting
underneath. Usually the majority of the spatter can be removed by striking a sharp blow followed by brushing with a
stainless steel wire (0.008 to 0.010 diameter)brush. Abrasive blasting may be required in some instances to dislodge
hard to remove spatter.
2-90
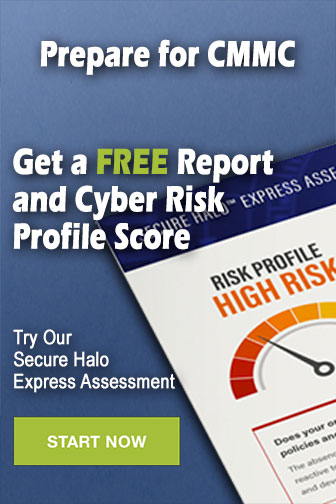