T.O. 1-1A-9
TABLE 2-15. WELDING CHARACTERISTICS - GENERAL, STEELS OTHER THAN STAINLESS (CONT'D)
6150
EAO18G
MIL-R-5632
6152
Class 2
8615
E9018G
MIL-R-5632
200°-300F
Normalize
Low hydrogen
8617
Class 2
type electrodes
8620
particularly
when low pre-
heat and inter-
pass tempera-
tures are em-
ployed are
generally used
for welding
this group.
8735
E10018G
MIL-R-5632
200°-300F
Normalize
Class 2
8630
E9018G
MIL-R-5632
300°-500°F
Stress Relief
Shielded-arc-
1100-1200F
carbon moly-
or Normalize.
bdenum elec-
trodes are re-
commended.
Bare electrodes
produce brittle
welds.
D-6-A
------
----------
450°-550°F
575-625, 1-1/2
Weldable in
hr cool in still
heavy section
air to 300F fol-
using normal
lowed by immedi-
techniques re-
ate stress relief.
quired for
Alternate, trans-
welding high
fer to furnace at
hardenable
preheat temp and
medium carbon
normalize at 1725-
low alloy steel.
1775, 30 minutes
Sections less
air cool.
than 0.125 in
some instances
may be welded
by the tungsten
inert gas pro-
cess without
pre-heating.
2-144. The medium carbon (AISI/SAE) grades of the low alloy steels are more difficult to weld than the low carbon
grades. If welding of this series is to be successful, close control of procedures is required. Preheating is necessary
except for thin 8630-4130, and even for these grades if shape of part/assembly is complicated. The medium carbon
grades in the as-welded condition are inherently brittle and require normalizing/stress relieving or heat treatment for
successful welding. In some instances for the welding of heavy section, intermediate stress relief is used by heating to
stress relief temperature from the pre-heat temperature, holding for 5-6 hours, and then lowering to preheat temperature
to complete the weld. After weld is completed, part is given a final stress relief or heat treated. For best results, stress
relief or heat treatment should be accomplished immediately after welding before material is allowed to cool below
minimum interpass/preheat temperature (for some alloys this is a mandatory requirement), and in any case before
material is allowed to cool to room or atmosphere temperature. Although thin material in grades 4130 and 8630 can be
welded without preheat, a preheat temperature of 200°-300°Fis recommended for best results.
2-86
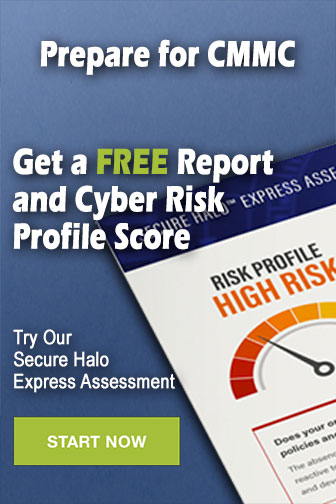