T.O. 1-1A-9
TABLE 2-18. FUSION WELDING CHARACTERISTICS OF CORROSION RESISTING STEEL - GENERAL(CONTD)
ALLOY/DESIGN
RECOMMENDED
FILLER MATERIAL/SPEC
HEAT TREATMENT
REMARKS
TYPE
STRUCTURE
TYPE
ELECTRODE
ROD
PREHEAT
POSTHEAT
MATERIAL
TREAT
305
Austenitic
308
MIL-R-5031
None re-
To restore
Not generally recom-
Class 1,
quired if
corrosion
mended for welding
above 60°
resistance and
reacts similar to 304
F.
to remove pre-
except due to higher
cipitation car-
nickel compared to
bide, heat
chromium (18-12) it
treat to 1850°
-
is more susceptible
2000
F), 1/2-
to cracking during
1 hr per inch
cooling.
thick and then
cool to below
800
F within
3 minutes
maximum by
quenching air.
310
Austenitic
310
MIL-E-6844
MIL-R-5031
None re-
Post annealing
Weldable by gas/or
Class 3,
Class 3,
quired if
required if
electricity prefer-
AMS 5075
AMS 5694
above 60
welded joint is
able by metal arc or
F.
to be exposed
inert gas arc methods.
to corrosive
Oxyacetylene is not
environment.
recommended be-
See Heat Treat
cause of carbon pick-
Data paragraph
up and resulting ad-
for tempera-
verse effect on cor-
ture.
rosion resistance.
316
Austenitic
316
MIL-R-5031
None re-
Anneal after
Subject to stress cor-
317
Austenitic
Class 4
quired if
welding. See
rosion and embrittle-
AMS 5691
above 60
Remarks and
ment when heated at
F.
General Heat
800
- 1600
F for pro-
Treat Data
longed period. Low
paragraph
carbon type 316L is
(2-74).
normally used for
cross sections which
cannot be annealed or
low temperature
stress relieved. Oxy-
acetylene welding is
not advisable for
casting because of
carbon pickup and
possible impairment
of corrosion resist-
ance. Metal arc pro-
cess is recommended
for welding, casting,
using lime coated
electrodes.
314
Austenitic
310
MIL-E-6844
MIL-R-5031
None re-
Anneal for
Can be welded by gas
Class 3,
Class 3,
quired if
maximum
or arc methods.
AMS 5695
AMS 5694
above 60°
corrosion re-
Material should be
F.
sistance. See
annealed after weld-
Heat Treat
ing to improve cor-
Data paragraph. rosion resistance.
2-95
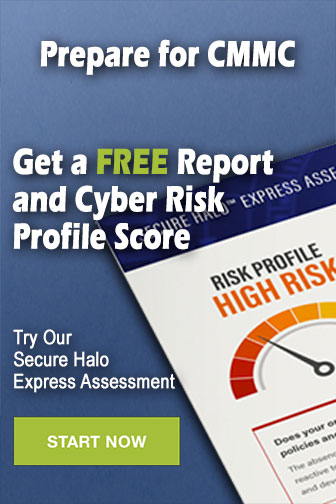