T.O. 1-1A-9
TABLE 2-18. FUSION WELDING CHARACTERISTICS OF CORROSION RESISTING STEEL - GENERAL(CONTD)
ALLOY/DESIGN
RECOMMENDED
FILLER MATERIAL/SPEC
HEAT TREATMENT
REMARKS
TYPE
STRUCTURE
TYPE
ELECTRODE
ROD
PREHEAT
POSTHEAT
MATERIAL
TREAT
420
Martensitic
420
MIL-E-6844
MIL-R-5031
4000 -6000F
1125°-1400
Welding should be
309
Class 2/3
Class 2/3
if possible
restricted to elect-
310
before mater-
rical method i.e.,
See Remarks
ial has cooled
shielded metal arc
to 300
F from
& tungsten arc, etc.
preheat and
Oxyacetylene welding
welding.
should be avoided to
prevent carburizing
and resulting loss
in corrosion resist-
ance. Type 309/310
electrodes can be used
if high strength not
required.
422
Martensitic
422
For inert
350
-400
F
1200
-1300
F
Can be welded by
gas method
for 8 hours,
metal arc or inert
air cool.
tungsten-arc method.
440
A, B,C & F
440
See Remarks
MIL-R-5031
450
F
1300
F for
Fusion welding should
309
Class 2/3
4 hours and
be accomplished using
310
air cool.
electrodes of same
composition as parent
metal when material
is heat-treated after
welding. If a softer
weld will meet re-
quirements, such as
welding for mechani-
cal bond only, type
309/310 electrodes
can be used.
446
Ferritic
446
300
F
1400
-1450°F
Fusion weld using
followed by
same composition as
air cooling/
parent metal. Weld-
water quench.
ing of this type is not
recommended for
applications subject
to high impact. For
improvement of
ductility in weld area,
weld deposit should
be preened while at
elevated temperature.
PH 15-7
PH15-
17-4 AMS
AMS 5825
Not re-
Heat treat or
See 17-7PH except
MO (AISI
7MO
5827 PH
AMS 5813
quired.
anneal.
for the following.
632)
PH15-
7MO
AMS 5812
Inert gas tungsten or
7MO
WPH15
fusion welding of
VM
7MO
annealed and subsequ-
VM
ently heat treated mat-
erial yields a weld of
80-100%. Resistance
flash butt welding is
not recommended for
joints to use in high
strength application.
2-97
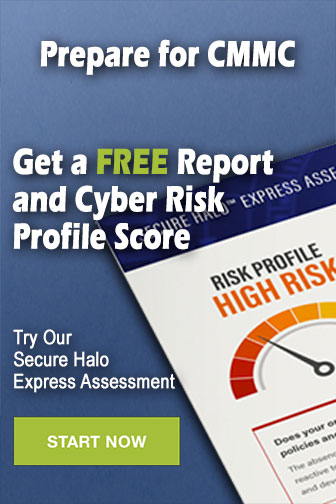