T. O. 1-1A-9
2-96. Lubrication for Milling. The lubrication of milling cutter is very important to control generation of heat which is
considerable in cutting all grades of stainless, and to prevent seizing of chips to cutting edges. The cutting oils used
should be applied in large quantities directly on the cutter and zone of cut. The sulphurized oils diluted to desired
viscosity with paraffin oil are usually satisfactory.
2-97. DRILLING CORROSION RESISTING STEEL.
High speed steel drills are commonly used for drilling stainless. Special types are used for drilling grades (420, 440, etc.)
that are abrasive due to high carbon content. Speeds for drilling the high carbon types are usually reduced 25-50% in
comparison to the other grades.
Drills for use with the corrosion resisting steels are 2-98. prepared with different cutting angles than used with carbon
steel. Drill point/tips for use with the chromium-nickel grades are usually ground with 135°-140° (included) angle and 8°-
15° lip clearance. The webb support for the point should be as heavy as possible; however, thinning of the webb at the
point will relieve point pressure. When drilling the free machining 400 series grades the angle is reduced to 118°-1300.
For general illustration of point designs see Figure 3-2.
2-99. Speeds used for drilling the corrosion resisting steels should be closely controlled to prevent hardening of metal
and excessive drill damage from heat. For suggested drilling speed using high speed steel drill bits, see Table 2-12.
Table 2-12. DRILLING SPEEDS FOR
CORROSION RESISTING STEEL.
GRADE TYPE
SPEED SFPM (APPROX)
301, 302, 304, 310
20 - 40
303
40 - 80
309, 316, 321, 347
30 - 50
403, 410
35 - 75
416, 420F, 430F
60 - 95
420 AB & C
20 - 40
442, 446
30 - 60
NOTE
Do not let drill ride on work to prevent work hardening and heat damage to drill. On larger
diameter drills use chip curling grooves to help expel and prevent chip accumulation in area
of hole being drilled.
2-100. Lubrication for Drilling Stainless. The recommended lubrication for general use and light drilling is soluble oil,
and for heavy work, sulphurized mineral or fatty oils. Utilization of adequate lubrication/coolant is of utmost importance
in drilling stainless due to poor heat conduction of this material.
2-101. REAMING CORROSION RESISTING STEEL.
The recommended reamer for the corrosion resisting steels is the spiral fluted type which is made from high speed
steel/carbide tipped. These spiral fluted reamers are used to help alleviate chatter and chip removal that are associated
with the straight fluted reamers.
2-102. Due to the work hardening characteristics of the corrosion resisting steel, it is advisable to leave sufficient stock
to insure that cutting will occur behind the work hardening surface resulting from drilling. The recommended material to
be left for reaming is 0.003-0.007 inch, and feed per revolution should be 0.003-0.005 for holes up to 1/2 inch and
0.0050.010 for reamers up to 1 inch diameter.
2-103. Reamers for cutting stainless should have a 260-300 starting chamfer with a slight lead angle behind the chamfer
of 10--2° for about 1/8-3/16 inch on the land to reduce initial shock of cutting.
The land should be ground with a clearance of 4°70 (and width should not be reduced below 0.0100.012 inch) to reduce
rubbing and frictional heat.
2-104. Speeds for reaming will vary according to type of material being cut. The recommended speed for reaming types
301, 302, 304, 316, 321, 347, 403 and 410 is 20 75 surface feet per minute; for 430F, 420F, 416, 440F and 303 -35 100
SFPM; and for 309, 310, 430, 431, 440, 442, 426 20-60 SFPM. Trial should be conducted to determine best cutting for
individual operations.
2-105. TAPPING CORROSION RESISTING STEEL.
Conventional or standard type taps are used with stainless; however, better results can sometimes be obtained by
modification of taps (in shop) as required and by use of two fluted type taps for small holes. For instance modification of
taps can be accomplished by grinding longitudinal grooves along the lands, omission of cutting edges on alternate
threads and relieving cutting edges will reduce binding and frictional drag.
These modifications will also aid in distribution of lubrication to cutting area, provide additional clearance for chips and
compensate for the swelling which is encountered with the softer temper material. The modification is usually
accomplished as follows:
1.
Longitudinal grooves are ground down the center of each land about 1/3 to 1/2 thread depth and 1/3 to 1/2
approximately of land width.
2.
Cutting edges are relieved by grinding a 2°50 radial taper on each land.
3.
Lands are narrowed by removing about half the threading area from each land. The portion removed should trail
the foremost cutting edge. Also, cutting edge should be ground to have positive hook/rake 15°-20° for softer material
and 10°0-15 for harder material.
2-75
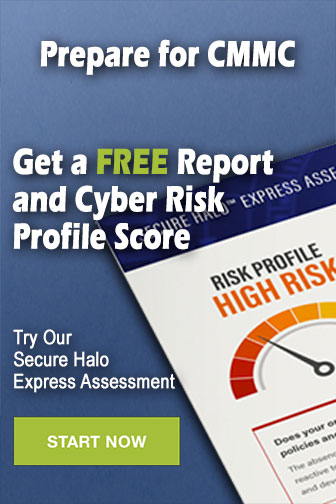