T. O. 1-1A-9
2-111. SAWING.
2-112. Hack saws (hand )for cutting corrosion resisting steel should be of high speed steel with approximately 32 teeth
per inch for light work and approximately 24 teeth per inch for heavy work. The teeth area should be of wavy
construction to increase width of cut area to prevent binding. As with cutting other metal, the blade should not be allowed
to drag/ride on the return stroke, especially with the 300 series types to prevent work hardening. The hack saw blade
should be lightly lubricated with lard oil/other cutting oil for best results.
2-113. Hack saws (mechanical drive). Power hack saws are used for heavy cross-cutting section bars, tubing, etc.
With the power hack saw, deeper cuts are made at relatively low speed. The deeper cuts are used to got under work
hardened surface resulting from previous cut (streke). The teeth per inch for saw blades average 8-12 and speed of saw
travel usually ranges from 50-100 feet per minute depending on type and temper of material being' cut. Coolant/
lubrication is essential to prevent excess blade damage from heat. Lubrication recommended is soluble oil/ water mixed
about 1 part oil to 4 parts water for heavy work, and for light work, a light grade cutting oil.
2-114. Band Sawing. Band saws are well suited for low speed (straight line/contour) sawing of stainless/corrosion
resisting steel within prescribed limitation. The saw manufacturer's recommendations should be followed for cutting
speed, saw selection, etc. However, speeds usually vary with the physical properties, temper, etc. , of type/grade being
cut. As general guide, speeds range from 100-125 feet per minute for material under 0. 062 and 60-100 FPM for
thickness over 0. 062 inch. Saw blades must be kept in sharp condition for effective low speed sawing.
2-115. For faster cutting with the band saw, the friction cutting method may be employed. In utilizing the friction
method, the band saw velocity ranges from 5000FPM for cutting flat 1/32 inch material to about 10,000 FPM for 1/2 inch
and 14,000'for I inch material; tubing material is run at slightly higher speed. Feed for this method can be considerably
higher than is used for slow speed cutting, rates range from about 100 FPM for light gauge to 15-18 FPM for 1/2 inch
material. Saw teeth per inch varies from 18for material below 1/8 inch thick to 10 per inch for thicknesses over 1/2 inch.
2-116. Heavy pressure to maintain cut is not usually necessary. Pressure should be just sufficient to create proper
heating and softening at cut point without forcing the saw. Lubricants should not be used.
2-117. WELDING . STEEL (GENERAL)
NOTE
For general welding procedures, see T. O. 34W4-1-5.
2-118. WELDING, TRAININGANDQUALIFICATIONS. Prior to citing details requiring control in welding, it is
appropriate to cite requirements for welders qualifications. Personnel assigned to accomplish welding shall be trained in
the handling of equipment, fabrication procedures, i.e., composition and identification of alloys, jigging, tacking, cleaning,
treating, blue print reading, safety, use of tools (hand and machine), and to meet qualification requirements.
2-119. Test for aircraft and missile welding operators qualifications are cited in Spec MIL-T-5021 and for welding
pressure systems in T.O. 00-25-224. The requirements set forth are intended to ascertain that welders engaged in
welding aircraft, aircraft parts and accessories, missiles, missile parts and accessories, and pressure systems/parts
possess and maintain a satisfactory level of proficiency. Periodic tests shall be made to assure that welders
qualifications are maintained in addition to test and inspection of parts as required by drawings, specifications, technical
orders and other technical data. The primary factors involved in the fabrication of any part is that it will meet
requirements set forth and this requirement shall not be waived because the work was accomplished by a qualified
welder or/person.
2-120. The welding of steels is related to individual characteristics of each type/grade. It is therefore essential to have a
working knowledge of the welding characteristics of each type. This point is emphasized by the fact that all grades are
affected in some manner by heat. The extent affected will depend upon the exposure time (dwell) and temperature
subjected. The results of heating such as in welding will change either physical or modify corrosion resistance properties,
or both.
2-121. Although each welding process presents problems which are peculiar, steels that have good welding
characteristics in one particular process generally can be welded by a s1milar process. Also it will be found that in a
particular process the method and source of heat contributes to a difference in response of the material to the welding
operation. For Instance, when gas is used as the heat source, slower temperature changed distributed over a wider area
prevail than when electricity is used.
2-122. Steels that are subject to high (air) hardening tendencies are the most difficult to weld and if the welding process
involves high temperature changes, the rate of cooling from the welding temperature must be controlled (retarded) if high
hardness and possible cracking in weld and heat affected area is to be avoided. To overcome this problem preheating of
the material is utilized and in some instances preheating and postheating are both employed to properly control heat treat
and corrosion resisting characteristics. For additional information on preheating/postheating of various alloys, see Table
2-15 and Table 2-18.
2-78
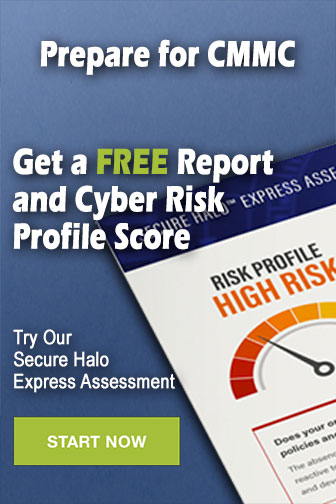