T. O. 1-1A-9
TABLE 2-7.
GENERAL MACHINING COMPARISON OF CORROSION RESISTING STEEL TO FREE MACHINING
SCREW STOCK B1112.
GRADE/TYPE
MACHINABILITY RATING
GRADE/TYPE
MACHINABILITY RATING
Group I 430F
80%
Group III 420
45%
416
75%
431
45%
420F
70%
440
45%
303
65%
442
45%
446
45%
347
40-45%
Group II 403
55%
Group IV 302
40%
410
50%
304
40%
430
50%
309
40%
440F
50%
316
40%
2-84. In machining of the corrosion resisting steels, difficulty will be experienced from seizing, galling and stringing. To
overcome these problems requires control of speeds, cutting tools, and lubricants. The following general practices are
recommended for shaping/grinding cutting tools, equipment, etc., for cutting corrosion resisting steel:
a.
Select tools of proper alloy/type and keep cutting edges sharp, smooth, free of burrs, nicks and scratches.
b.
Avoid overheating cutting tool when grinding to prevent surface and stress cracking.
c.
Grind tools with generous lip rake and with ample side and front clearance.
d.
Speeds are critical in machining stainless; select speed about 50% slower than those used for carbon steels as a
starting point.
e.
In general, use slow speeds and heavy feed to reduce effect of work hardening. Avoid riding of tool on work and
intermittent cutting when possible.
f.
Apply proper lubricant/coolant to cutting tool to prevent overheating.
g.
Support cutting tool rigidly near work to prevent lash and other difficulty from use of heavy cutting feeds.
2-85. Cutting Tools for Machining Corrosion Resisting Steels. Selection of cutting tool is important for machining
stainless due to tough machining characteristics. The following is a recommended guide for selection of tools: a. For
general machining and short runs use high speed tool steels such as Tungsten Type T1 (18-41) and Molybdenum-
Tungsten Type M3 (6-6-3).
a.
For general machining and short runs use high speed tool steels such as Tungsten Type T1 (18-41) and
Molybdenum-Tungsten Type M3 (6-6-3).
b.
For medium runs at approximately 25% higher speed, use Tungsten-Cobalt Type T5 (18-4-2-8) and2.71
Tungsten-Cobalt Type T4.
c.
For long production runs at high speed, use Tungsten Carbides. Cutting tool of these alloys can be used at
approximately 100% faster speeds than the Tungsten-Cobalt type.
NOTE
Some types of tool steel are available in raw stock IAW Federal Specifications, see paragraph
7-4. Prior to attempting local manufacture of cutting tools, facilities/ equipment must be
available to properly heat treat. In addition, from an economic standpoint, it is usually
advisable to obtain most cutting tools prefinished to size, etc., and heat treated.
2-86. TURNING OF THE CORROSION RESISTING STEELS.
2-87. Tools for turning the corrosion steels should be ground with a heavy side rake clearance for maximum cut
freedom. The upper surface of the tool should be finished with a fine wheel or hand stoned to prevent galling. For chip
disposal or breakage a chip grove is usually necessary except with the free machining grades. In addition, the chip
breakage is a safety precaution to prevent difficulty and hazards in breaking the expelled cutting. Do not allow tools to
become dull to prevent surface hardening from rubbing and hard spots which are difficult to remove.
2-71
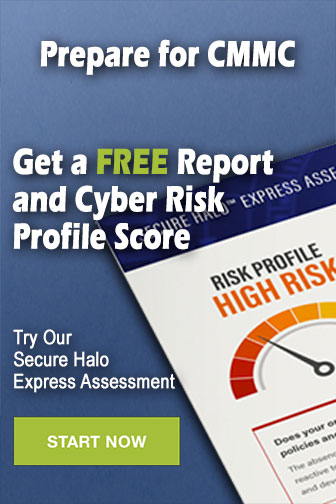