T.O. 1-1A-9
Figure 8-6. Shore Scleroscope
b.
A vertical glass tube, mounted to the base and
containing the cylindrical diamond point hammer.
c.
A suction heat and bulb for lifting and releasing
the hammer.
d.
A scale, visible through the glass tube, for
determining the height of the rebound.
e.
A magnifier hammer with a larger contact area
is supplied for use with extremely soft metals.
8-20. TESTING WITH THE SCLEROSCOPE. The test
is made as follows:
1.
Level the instrument by means of the adjusting
screws (1). (See figure 8-6). The level position is
determined by means of the plumb rod (2).
2.
Prepare the test specimen as described for the
Brinell and Rockwell tests in preceding paragraphs and
clamp it on the base. This is done by raising the lever
(3) inserting the sample and exerting the pressure on
the clamping show (4).
3.
Raise the hammer (5) by squeezing and
releasing the bulb (6).
4.
Release the hammer by again squeezing the
bulb and observing its rebound.
5.
Several tests should be made at different points
of a specimen, and an average reading taken to reduce
visual error.
8-21. TENSILE TESTING. The terms tension test and
compression test are usually taken to refer to tests in
which a prepared specimen is subjected to a gradually
increasing load applied axially until failure occurs. For
the purpose of tensile testing implied by this technical
order this type of setting would apply to determining the
mechanical properties desired in a material. For this
test, the following test specimens are listed. (See
Figure 8-7.) This does not exclude the use of other test
specimens for special materials or forms of material.
The tensile strength shall be determined by dividing the
maximum load on the specimen during a tension test by
the original cross-sectional area of the specimen.
1.
Diameter of the reduced section may be smaller
at center than at ends. Difference shall not exceed 1%
of diameter at ends.
2.
When an extensometer is required to determine
elastic properties, dimensions C and L may be modified.
In all cases the percentage of elongation shall be based
on dimension G.
3.
The type R1 test specimen is circular in cross
section and is used for bars, rods, forgings, plates,
shapes, heavy-walled tubing, and castings. Types R2,
R3, R4, & R5 are circular in cross-section and are used
for material of dimensions insufficient for type R1.
1.
The ends of the reduced section shall not differ
in width by more than 0.004 inch.
2.
The ends of the specimen shall be symmetrical
with the center line of the reduced section within 0.10
inch.
3.
When material is over 2 inches thick, machine
to 3/4 inch or use type R1 test specimen. For more
detailed information, refer to Federal Test Method
Standard No. 151.
8-22. DECARIURIZATION MEASUREMENT.
8-23. Decarburization is the loss of carbon at the
surface of ferrous materials which have been heated for
fabricating, welding, etc., or when heated to modify
mechanical properties. Effective decarburization is any
measurable loss of carbon content which results in
mechanical properties below the minimum acceptable
specifications for hardened materials. The most
common methods used to measure decarburization are
microscopic, hardness and chemical. The microscopic
method is sufficiently accurate for most annealed and
hot rolled material for small amounts of decarburization
in high carbon (over 0.60%), high hardness steels.
8-8
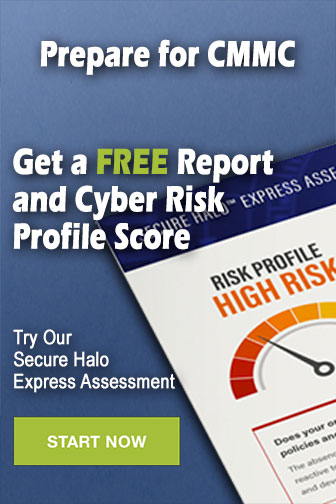