T.O. 1-1A-9
8-27. NONDESTRUCTIVE INSPECTION METHODS.
8-28. Radiographic inspection will show internal and external structural details of all types of parts and materials. It is
accomplished by passing penetrating radiation (usually X or gamma rays) through the part or assembly being inspected
to expose a film. After developing, interpretation of the radiograph will indicate defects or damage. All radiographic
inspections shall be accomplished in accordance with T.O. 33B-1-1, MIL-STD-453, and MIL-STD-410.
8-29. Penetrant inspection is a nondestructive inspection method that is used to detect discontinuities open to the
surface of nonporous material.
It is accomplished by treating the inspection area with a fluid (penetrant) that penetrates the surface discontinuity.
Surplus penetrant remaining on the surface is removed and an absorbent material (developer) is applied to the surface.
The developer acts as a blotter and draws some of the penetrant from the discontinuity to the surface. Discontinuities
are visible due to color contrast between the penetrant drawn out and the background surface.
Only fluorescent penetrants are approved for Air Force use. All penetrant inspection materials shall conform to MIL-I-
25135. All penetrant inspections shall be accomplished in accordance with T.O. 33B-1-1 and MIL-STD-410.
8-30. Ultrasonic inspection uses a high frequency sound wave to detect discontinuities in materials. The pulser in the
ultrasonic instrument sends an electrical impulse to a piezoelectric material in the search unit (transducer). The
transducer changes the electrical impulse into mechanical vibrations (sound) and transmits them into the material being
inspected. Any marked change in acoustic properties, such as a flaw or interface in the material, reflects the sound back
to the transducer. Examination of the reflections on a cathode ray tube will reveal discontinuities in the material. All
ultrasonic inspections shall be accomplished in accordance with T.O. 33B-1-1, MIL-I-8950, and MIL-STD-410.
8-31. Magnetic particle inspection is used to detect discontinuities in ferromagnetic materials, principally iron and steel.
Magnetic particle inspection is accomplished by inducing a magnetic field into the material being inspected. A
discontinuity will interrupt this field, creating north and south poles which will attract magnetic particles applied to the
material. Discontinuities are visible due to color contrast between the magnetic particles and the background surface.
All magnetic particle inspections shall be accomplished in accordance with T.O. 33B-1-1 and MIL-STD-410.
8-32. Eddy current inspection is used to detect discontinuities in materials that are conductors of electricity. An eddy
current is the circulating electrical current induced in a conductor by an alternating magnetic field, which is produced by a
small test coil in contact with or close i the material being inspected. Discontinuities in the material being tested cause
variations in the induced eddy current. The test coil measures the variations which reveal discontinuities in the material.
All eddy current inspections shall be in accordance with T.O. 33B-1-1 and MIL-STD-410.
8-33 thru 8-39. Deleted.
8-40. CHEMICAL ANALYSIS. Chemical analysis methods are those in which the elements present in metals are
determined by the use of reagents in solution, by combustion methods, or by other none-mission methods. Sample
metal from any piece shall be such that it represents as nearly as possible the metal of the entire piece. Drilling, milling
and other machining operations for sample metal shall be per formed without the use of water, oil, or other lubricants,
and cutting speeds shall be such that no burning takes place to cause alternation of the chemical composition of the test
metal. Method IlI.I of Federal Method Standard 151A is the controlling document for chemical analysis.
8-41. SPECTROCHEMICAL ANALYSIS. Spectrochemical analysis includes all methods in which measurements of
electromagnetic radiations produced by a sample metal are employed to determine the chemical composition. Samples
shall be so selected as to be representative of the entire quantity of metal under inspection. Cutting speeds in all
machining operations shall be such that no burning takes place to cause alteration of the chemical composition of the
test metal. Method 112.1 of Federal Test Method Standard 151A governs this type of analysis. The result of
spectrochemical analysis shall be determined to the number of decimal places shown in the chemical requirements for
the material.
Change 4 8-13/(8-14 Blank)
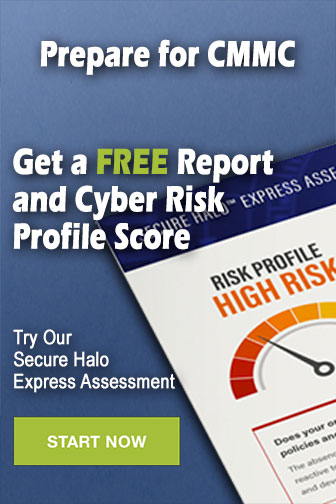