T.O. 1-1A-9
Figure 8-3. Attachments for Rockwell Tester
indication of hardness of a given part, several readings (3-6 is usually sufficient) at different points should be taken and
averaged. If it is necessary to determine the condition of the interior, parts should be cut by some method that does not
appreciably change the temper/ condition, such as using a water-cooled saw-off-wheel. When testing clad material; the
clad coat shall be removed. Specimen samples of clad and other materials should be provided when possible. It is not
desirable to accomplish the test on the finished part.
8-13. The Rockwell testers are equipped with various anvils and indentors. Typical anvils and attachments are shown in
Figure 8-3. The anvil (a) should be properly selected to accomplish the job. The tester should also be properly set and
in good working order before making any test. The table on which the Rockwell tester is mounted must be rigid and not
subject to any vibration if accurate results are to be obtained.
8-14. The accuracy of the Rockwell hardness tester should be checked regularly. Test blocks are available for testing
all ranges of hardness. If the error in the tester is more than 2 hardness numbers, it should be re-calibrated. The dash-
pot should be checked for oil and properly adjusted for completion of travel. The bell indentor and diameter should also
be checked regularly for bluntness and chipping and replaced as required.
8-15. VICKERS PYRAMID HARDNESS TEST. The Vickers pyramid hardness test (Figure 8-4) covers a normal range
of loading from 2.5 to 127.5 kilograms. However, for special applications,. such as the hardness testing of thin, soft
materials, loads as low a 50 to 100 grams may be used. This test made by pressing a square base diamond indentor into
a flat surface of the metal being tested by the application of known pressure. The indentation left by the indentor is a
square, the diagonal of which remains the hardness of the metal. The diagonal of the square impression is measured by
a microscope which reads directly to 0.001 millimeters on a large micrometer drum. With the standard pyramidal
diamond indentor (Figure 8-5) having an angle of 1360 between opposite face of the pyramid, the pyramidal hardness
number is determined by dividing the applied load in kilograms by the pyramidal area of the impression in square
millimeters by the formula,
Hardness
1.854
applied load in kilograms
square of the diagonal of impression
or from correlation tables accompanying the tester.
Rapid readings may be taken by means of three knife edges in the field of the eye-piece. The first knife edge is fixed;
the second knife is movable through a micrometric screw connected to a counter. The third knife edge, moved by means
of a special screw, may be used if rapid reading of values to specified limits is desired. This method of testing is highly
flexible and permits testing for very high hardness values. In the Amsler-Vickers variation of this hardness tester the
surface of the material to be tested, at which the indentor contacts may be thrown on a ground-glass screen directly in
front of the operator, allowing the length of the diagonals to be read directly.
8-16. Vickers Tester. The Vickers tester consists of the following major parts:
a.
Table for supporting the metal to be tested.
b.
A lever with a 20 to 1 ratio through which a load is applied through a rod to an indentor at the end of a tube
moving up and down in a vertical position.
c.
A frame continuing a control in which a plunger moves up and down vertically under the influence of a cam
which applies and releases the test load. The cam is mounted on a drum and when the starting handle is
depressed, the whole is rotated by a weight attached to a flexible cable, the speed of rotation being controlled by
a piston and dashpot of oil. The mechanism provides for a slow and diminishing rate of application for the last
portion of the load.
8-5
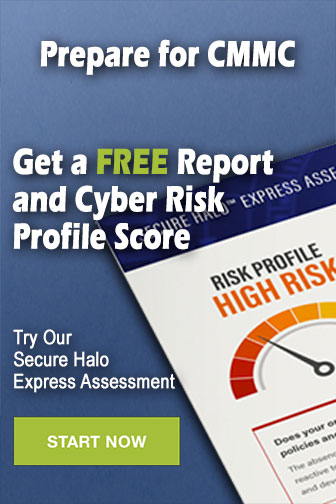