T.O. 1-1A-9
SECTION VIll
TESTING AND INSPECTION
HARDNESS TESTING
8-1. GENERAL.
8-2. Hardness testing is used to determine the results of heat treatment as well as the state of the metal prior to heat
treatment. Its application in determining the approximate tensile strength of the material by use of a hardness-tensile
strength table is very limited and should only be used in the case of ferrous (steel) alloys. Table 8-1 should be used only
as a conversion table for converting the various hardness values from one type of test to another, and should not be
used as an indication of tensile strength for alloys other than ferrous. In addition, it should be realized that values given
in Table 8-1 are only approximate. Whenever a specific type of hardness test is given in a drawing, specification, etc.,
necessary hardness readings should be made by that test whenever possible, rather than by other means, and a
conversion made. In obtaining hardness value, precaution must be taken to assure removal of elod1ing and
decarburized surface layers from area to be tested.
8-3. METHODS OF HARDNESS TESTING.
8-4. The methods of hardness testing in general use are: Brinell, Rockwell, Vickers (British), Tukon and Shore
scleroscope.
8-5. BRINELL HARDNESS TEST. This test consists of pressing a hardened steel bill into a flat surface of the metal
being tested by the application of a known pressure. The impression made by the ball is measured by means of a
microscope with a micrometer eyepiece. The Brinell "number" is obtained by dividing the load in kilograms by the area
of the spherical impression made by the ball, measured in square millimeters. The thickness of all samples used for
testing must be sufficient to prevent bulging on the under side.
8-6. Brinell Tester. The Brinell tester (Figure 8-1) consists of the following major parts:
a.
An elevating screw and anvil for bringing the sample into contact with the ball.
b.
A manually operated hydraulic pump for applying the pressure to the hardened steel ball, which is mounted on its
actuating member.
c.
A pressure gage for determining the applied pressure.
d.
A release mechanism with micrometer eyepiece for calculating-the area of the impression.
8-7. Making The Brinell Test. The test is preformed as follows:
1.
Prepare the sample by filing, grinding, and polishing to remove all scratches and variations that may affect the
reading.
2.
Place the sample on the anvil of the machine and elevate until the hardened ball contacts the surface to be
tested.
3.
Apply the load by pumping handle.
NOTE
A load of 3,000 kilograms is required for steel, while 500 kilograms is used when testing the
softer metals, such u aluminum alloy, brass, and bronze. Normally, the load should be
applied for 30 seconds. although this period may be increased to 1 minute for extremely hard
steels, in order to produce equilibrium.
4.
Release the pressure and measure the area of impression with the calibrated microscope.
5.
Calculate the Brinell number, completing the test.
8-8. ROCKWELL HARDNESS TEST. The Rockwell hardness test is based on the degree of penetration of a specifically
designed indentor into a material under a given static load. The indentor/penetrator used may be either a diamond or
hardened steel ball, The diamond indentor called a "brale" is precision ground and polished and the shape is
spheroconica. The steel ball for normal use is 1/16 inch diameter, however, other larger diameter steel ball such as 1/8,
1/4 or 1/2 inch may be used for testing soft metal. The selection of the ball is based on the hardness range of the type of
material to be tested.
8-9. The Rockwell machine/tester for accomplishing the hardness test applies two loads to obtain the controlled
penetration and indicates results on a graduated dial (see Figure 8-2). A minor load of 10 kilograms is first .applied to
seat the penetrator in the surface of the test specimen. The actual penetration is then produced by applying a major
load, subsequently, releasing and then reading hardness number from the dial. The dial reading is related to the depth of
penetration, load and the penetrator used. The shallower the penetration, the higher the hardness value number for
given indentor and load. The normal major lead is 150 kilograms ("C" Scale) when using the diamond penetrator and
100 kilograms ("B" Scale)
8-1
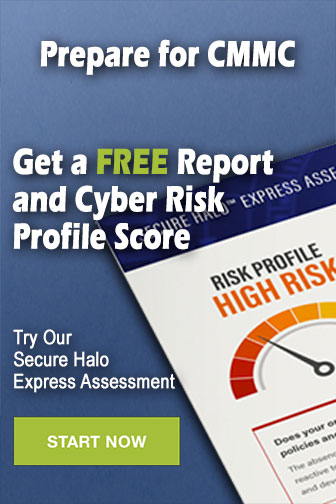