T.O. 1-1A-9
5-43. Non-consumable tungsten electrodes, 1/32inch to 1/8 inch diameter, may be used with or without filler metal as
desired. When filler metal is desired, the use of AMS4951 rod is recommended.
5-44. CLEANING. As in the welding of other metals, the surface of titanium must be clean prior to welding operations.
Grease oil, dirt, and scale must be removed by solvent degreasing, chemical pickling, grit blasting, grinding, wire
brushing or a combination of these treatments. Solvent degreasing may be accomplished using hot trichloroethylene
(180°F). Either wet or dry grit blasting may be used. The pickling solution most recommended is a mixture of 20 to
307% nitric acid and hydroflouric acid mixed in water. The ratio of nitric to hydrofluoric acid should be at least 15 to 1 to
minimize hydrogen pick up. Precautions will be taken to keep the nitric acid content from dropping below its normal
range, since a nitric content below 10% will result in hydrogen embrittlement.
5-45. SPOT AND SEAM WELDING . Effective joining of titanium with this method of welding can be accomplished
without the difficulty experienced with other types of welding. Excessive penetration is the only characteristic requiring
control, since the welds are less ductile than the base metal. Trial is advised by obtaining set-up pieces from the same
lot of material as the parts to be welded so that penetration may be limited.
5-46. Protective atmosphere control, which is usually required with other types of welding, of titanium is not necessary
and for most practical purposes the welding conditions, electrode pressures, current settings and times are essentially the
same as those used for stainless steel, except for seam welding. The electrode force should be reduced slightly for
seam welding as compared to stainless steel. See paragraph 2-170 through 2-193 for general requirements regarding
spot/seam welding and Table 5-5 for minimum required shear strength per weld for spot weld shear specimens and
minimum average strength and titanium and titanium base alloys. This data was obtained from Specification YIL-W-
6858.
5-47. BRAZING. To braze titanium and its alloys, special atmospheres and fluxes are required; however, ordinary
furnace, torch induction, or resistance procedures can be utilized. Furnace and induction brazing can be done without
fluxes in a vacuum of an inert atmosphere. Without atmospheric protection, special fluxes developed especially for
titanium are required. Generally these fluxes are composed of a mixture of fluoride and chlorine in various percentages.
5-48. To prevent alloying between the titanium and the brazing alloy, rapid heating cycles should be employed. Excess
mixing (alloying) will cause the formation of brittle phases at the joints. Since induction brazing is faster than furnace
brazing, this is the method recommended. The most satisfactory filler metal is fine silver. Joints brazed with fine silver
have better strength and ductility than those prepared with silver-base alloys. The brazing method can be used to join
titanium to other metals, but precoating is required to obtain a satisfactory joint. The strength of the joints is lower than
those that are obtained by brazing titanium to titanium.
5-49. SOLDERING. Limited information is available on soldering. It is possible to successfully solder titanium where
little strength is required, by precoating with a thin film of silver, copper or tin from their chloride salts. This can be
accomplished by heating the chloride salts-coated titanium in an atmosphere controlled furnace as previously mentioned
in paragraph 5-18. The resultant film should be made wet with either a 6OW tin-40% lead or a 50%-50%tinandlead
solder. Since the deposited film may dissolve in the liquid solder and dewet the surface, it is important that the time and
temperature be held to a minimum.
5-50. RIVETING. Riveting of titanium can be accomplished using conventional equipment with rivets manufactured
from commercially pure material; however, the rivet holes require close tolerances to insure good gripping. The driving
time is increased about 65% over that required for high strength aluminum rivets. Better results can be obtained by
using the squeeze method rather than the rivet gun and bucking bar. When it is necessary to have flush-head rivets,
dimpling can be accomplished at temperatures of 500°F to 700°F. Other types of rivets such as high strength aluminum,
stainless steel and monel are also used to join titanium.
5-51. Due to difficulties involved, the above mentioned method will probably be replaced inmost cases with rivets of the
high shear series, i.e., pin rivets such as NAS1806 through NAS1816, tension rivet NAS2006through NAS-2010, and
shear rivet NAS-2406 through NA8-2412.
5-52. As with other metals, it is necessary to take precautions to avoid galvanic corrosion when titanium is riveted to
other metals. This can be accomplished by coating the titanium with zinc chromate primer Specification MIL-P-8585.
Change 12
5-13
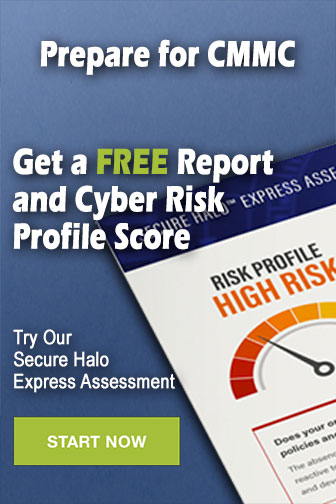