T.O. 1-1A-9
SECTION VI
COPPER AND COPPER BASE ALLOYS.
6-1. COPPER AND COPPER BASE ALLOYS.
6-2. Most of the commercial coppers are refined to a purity of 99.90%, minimum copper plus silver. The two principal
copper base alloys are brass and bronze, containing zinc and tin respectively, as the major alloying element. Alloy
designations for wrought copper and copper alloys are listed in table 6-1, with the corresponding specification and
common trade names.
6-3. COPPER ALLOYING ELEMENTS.
ZINC - Added to copper to form a series of alloys known as brasses. They are ductile, malleable, corrosion resistant and
have colors ranging from pink to yellow.
TIN - Added to copper to form a series of alloys known as bronzes. Bronzes are a quality spring material, and are strong,
ductile and corrosion resistant.
LEAD - Added to copper in amounts up to 1% to form a machinable, high-conductivity copper rod. It is added to brasses
or bronzes in amounts of 0.5 to 4% to improve machinability and in the range of 2 4% to improve bearing properties.
ALUMINUM - Added to copper as a predominating alloy element to form a series known as aluminum bronzes. These
alloys are of high strength and corrosion resistance.
IRON - Added to copper along with aluminum in some aluminum bronzes and with manganese in some manganese
bronzes.
PHOSPHOROUS - Added to copper principally as a deoxidizer and in some bronzes to improve spring properties.
NICKEL - Added to copper for higher strength without loss of ductility. They have excellent corrosion resistance.
SILICON - Added to copper to form the copper silicon series having high corrosion resistance combined with strength
and superior welding qualities. Small amounts are used as deoxidizers.
BERYLLIUM - Added to copper to form a series of age hardenable alloys. In the fully treated condition, it is the strongest
of the copper base alloys and has an electrical conductivity of 20%. Beryllium-coppers are widely used for tools where
non-sparking qualities are desired.
MANGANESE - Added primarily as a desulfurizing and de-gassifying element for alloys containing nickel.
6-4. CHEMICAL COMPOSITION The chemical composition of the copper alloys (listed by commercial trade name) is
listed in table 6-1.
6-5. HEAT TREATMENT AND NOT WORKING TEMPERATURE OF COPPER ALLOYS.
6-6. During production and fabrication, copper alloys may be heated for homogenizing, hot working, stress relief for
solution treatment, and precipitation hardening. The temperatures commonly used for heating, hot working and
annealing after cold working are given in table 6-2.
6-7. STRESS RELIEF OF COPPER ALLOYS.
6-8. Table 6-3 below gives a list of typical stress relief treatments commonly used in industry. This table is listed in
terms of chemical composition percents, and should be used as representing average stress relieving temperatures.
6-9. MACHINING COPPER AND COPPER ALLOYS. Free cutting brass is one of the most easily machined metals and
serves as a standard for machinability ratings of copper alloys. The following table gives the machinability ratings and
recommended speeds and feeds for use with high speed steel tools.
6-10. WROUGHT-COPPER-BERYLLIUM ALLOYS. The beryllium copper alloys are frequently used due to their ability
to respond to precipitation or age hardening treatments and other beneficial characteristics. Some of the characteristics
are; good electrical and thermal conductivity, high strength hardness, corrosion resistance, good wear resistance, non-
magnetic qualities and very good fatigue strength.
6-1
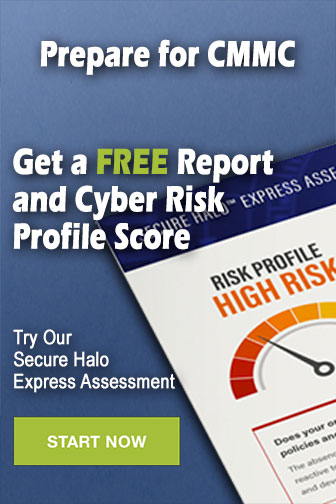