T.O. 1-1A-9
TABLE 5-9. ANGLES FOR TOOL GRINDING
ANGLES
CAST ALLOY TOOL
CARBIDE TOOL
Axial Rake
0°
0°
Radial Rake
0°
0°
Corner Angle
30°
60°
End Cutting
Edge Angle
6°
6°
Relief
12°1
6-10°1
5-68. TAPPING. Due to the galling and seizing that are characteristic of titanium, tapping is one of the more difficult
machining operations. Chip removal is one of the problems that will require considerable attention in an effort to tap
titanium. Another problem will be the smear of titanium. Build up from smear will cause the tap to freeze or bind in the
hole. These problems can be alleviated to some extent by the use of an active cutting fluid such as sulphurized and
chlorinated oil.
5-69. Power equipment should be used when possible and a hole to be tapped should be drilled with a sharp drill to
prevent excessive hardening of the hole wall. In the attempt to tap titanium, difficulties involved can be minimized by
reducing the thread to 55 or 65% from the standard 78%.
5-70. The following are procedures and material recommended for tapping titanium.
a. Cutting speed: 40 to 50 FPM for unalloyed and 20 to 30 FPM for the alloy grades.
b. Type of Tap: Gun or spiral point, 2 fluted in sizes 1/4-20 or less; 3 fluted in sizes greater than 1/4-20.
c. Cutting fluid; Active cutting oil such as oil, cutting, sulfurized mineral, 8peciilcation VV-0-283, Grade 1.
5-71. REAMING. Preparation of the hole to be reamed and the type of reamer used is the key-note to successful
reaming operations. As with tapping operations, the hole to be reamed should be drilled with a sharp drill. A straight-
fluted reamer can be used, but spiral-fluted reamers with carbide tips usually produce the best results. Speeds of 40-200
FPM and feeds of 0.005 to 0.008 inch are satisfactory; however, these factors depend on the size of the hole. Feeds
should increase in proportion to the size of the hole. The removal of larger amounts lessens the degree of concentricity.
If the degree of concentricity is an important factor, smaller amounts should be removed.
5-72. GRINDING. The essential requirements for grinding are the selection and use of grinding fluids and abrasive
wheels. Grinding of titanium is different from grinding steel in that the abrasive grain of the wheel wears or is dissolved
by a surface reaction, rather than wheel wear which is caused by breakage. To overcome this problem, lower wheel
speeds and the use of aluminum oxide or soft bonded silicone carbide wheels employing wet grinding methods are
recommended. Recommended wheel speeds are: 1500-2000 SFPM and table feeds of 400 to 500 inches per minute
with down feed of 0.001 inch maximum per pass and using 0.05 inch cross feed for highest grinding ratios.
5-17/(5-18 Blank)
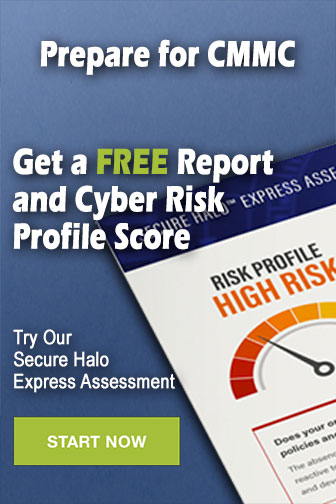