T.O. 1-1A-9
5-27. FABRICATION.
5-28. FORMING SHEET METAL-GENERAL . The forming of the unalloyed titanium can be accomplished at room
temperature using approximately the same procedures as those established for 18-8 stainless steel. The basic
difficulties encountered are sheet thickness, property variations, direction of grain flow and flatness. The above factors
combined with high yield strength, high tensile strength and low uniform elongation of commercial titanium alloys makes
forming difficult. The current equipment available was designed for material of uniform quality and considerable work is
required for adaptation to form titanium.
5-29. BENDING. Straight-Edge Bending of titanium using power brake on hand forming equipment can be
accomplished to a limited degree using the methods developed for stainless steel. The factors which require control are
the compensation for spring back and the bend radii. Springback is comparable to that of hard stainless steel when
formed at room temperature. The bend radii will depend on the type of material or alloy and whether forming is
accomplished hot or cold. The forming of material requiring tight bends or small radii necessitates the application of heat
in the range of 500°F. The heat should be applied for only short periods of time to avoid excessive oxygen and nitrogen
contamination which causes embrittlement. For approximate cold bend radii of sheet titanium see Table 5-4. Actual
practice may reveal that smaller bend radii can be used.
5-30. DRAW FORMING. Deep draw forming should not be attempted unless adequate equipment and facilities are
available. This will require that facilities be maintained for heating and controlling temperatures of the blanks to be
formed and the dies used in the forming operation.
5-31. HYDRAULIC PRESS FORMING . Rubber pad hydropress forming can be accomplished either hot or cold'
depending on the type tooling employed and the press pressures used. This type of forming is used on parts that are
predominately flat and have flanges, beads, and lightening holes. A male form block is set on the lower press platen and
the blank held in place on the block by locating pins. A press-contained rubber pad (45 to 55 Shore Durometer hardness
and about 8 inches thick) is located over the form block and blank. The press is then closed. As the ram is lowered, the
rubber pad envelops the form block forcing the sheet metal blank to conform to its contour.
5-32. Many parts can be formed at room temperature on the hydropress if flange clips, wedges and hinge-type dies are
used. When cold forming is employed, it is usually desirable to partially form the parts, stress-relieve at 1000°F for 20
minutes, then finish form. Hot forming for severely contoured parts or when only low-forming pressures are available is
accomplished between 600°F and 800°F. For this procedure, the form block is heated to the required temperature, the
blank positioned and covered with powdered or shredded asbestos; then a rubber pad 70 to 80 Durometer hardness is
placed on top. This extra pad of rubber serves two purposes: First, it provides additional rigidity for forming; and second,
it protects the press-contained rubber from the hot form block.
5-33. Tooling for hydropress form blocks, if elevated temperature forming is to be used, requires that pressure plates and
dies be made somewhat thicker than in normal practice. If long runs are anticipated, it is recommended that form blocks
be made from a good grade 'of hot-work tool steel due to the galling action of titanium at elevated temperatures.
5-34. STRETCH FORMING . Stretch forming has been used on titanium primarily to bend angles, hat sections, Z-
sections and channels and to stretch form skins so that they will fit the contour of the airplane fuselage. This type of
forming is accomplished by gripping the section to be formed in knurled jaws, loading until plastic deformation begins,
then wrapping the part around a female die. This operation is performed at room temperature and should be done at a
very slow rate. Spring back is equivalent to that of ¼ hard 18-8 stainless steel. All blanks for stretch-forming should
have the edges polished to remove any notch effects. Approximately 0.025 inch of sheared edges should be removed.
5-35. DROP-HAMMER FORMING . Drop-hammer forming of titanium has been very successful and has been
accomplished both at room and at elevated temperatures. Kirksite is satisfactory for male and female dies where only a
few parts are required. If long runs are to be made, ductile iron or laminated steel dies are usually necessary. In drop-
hammer forming, the best results have been obtained by warming the female die to a temperature of 2000 to 300SF to
remove the chill and heating the blank to a temperature of 800°-1000°F for 10 to 15 minutes. The part is then struck and
set in the die. Usually a stress relief operation at 1000°F for 20 minutes is necessary, then a re-strike operation. In most
instances, a finished part requiring no hand work is obtained.
5-8
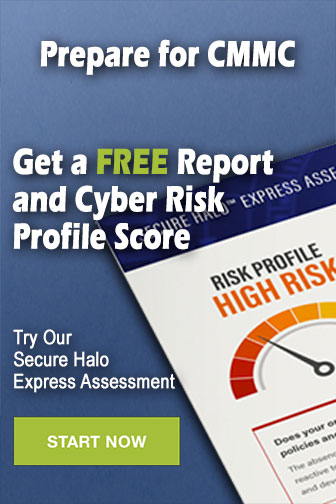