T.O. 1-1A-9
5-19. Air-chamber furnaces are more flexible and economical for large volumes of work and for low temperature heat
treatments; but at high temperatures where surface oxidation (above 1000°F) is significant, a muffle furnace utilizing
external heating gives more protection, especially if gas heated. For general use, electric furnaces are preferred since
heating can be accomplished internally or externally with a minimum of contamination. Furnaces which have given
satisfactory results are vacuum furnaces capable of supplying pressures of one micron or less; and inert gas furnaces
which control the atmosphere to 1% or less of oxygen and nitrogen combined.
NOTE
Avoid direct flame impengement to prevent severe localized oxidation and contamination.
Also avoid contact with scale or dirt.
5-20. Alternately direct resistance heating may be used where extremely short heat up cycle on nearly finished parts is
required to minimize surface oxidation.
5-21. The commercially pure, or unalloyed titanium, can only be hardened/strengthened by cold work. Stress relief and
annealing are the only heat treatments applicable to these alloys. These processes of heat treatment are employed to
remove residual stress resulting from grinding, work hardening, welding, etc.
For recommended temperatures and times see Table 5-3.
5-22. The soaking period for heat treatment of titanium alloys shall be the minimum necessary to develop the required
mechanical properties. The minimum soaking period (when unknown) shall be determined by test samples run prior to
heat treating the finished material or part. Excessive heat treat soaking periods shall be avoided to prevent diffusion of
oxygen hydrogen and nitrogen. Oxygen and nitrogen diffusion will take the form of a hard brittle surface layer which is
difficult to distinguish from the base metal. The brittle layer must be removed by mechanical or chemical means prior to
forming or application in stressed components. For the recommended soaking periods and temperatures see Table 5-3.
5-23. Scaling (oxidation) of titanium and titanium alloys starts at about 900°F. Light scaling which forms from exposure
to temperatures up to 1000°F has little or no detrimental effect on mechanical properties. Heating to temperatures above
1000°F under oxidizing conditions results in severe surface scaling as well as diffusion of oxygen.
5-24. HYDROGEN EMBRITTLEMENT . Hydrogen embrittlement is a major problem with titanium and titanium alloys.
Hydrogen is readily absorbed from pickling, cleaning and scale removal solution at room temperature and from the
atmosphere at elevated temperatures. Hydrogen embrittlement in the basically pure and alpha alloys is evident by a
reduction in ductility and a slight increase in strength. This is associated with a decrease in impact strength at
temperatures below 200°F and a shift in the temperature range where the change from ductile to brittle occurs. With
alpha-beta alloys, embrittlement is found at slow speeds of testing and under constant or "sustained" loads as
demonstrated by tests on notched specimens. This type of embrittlement, which is similar to the embrittlement of steel,
only becomes evident above a certain strength level. Solution heat treating and aging the alpha-beta alloys to high
strength levels increases sensitivity to hydrogen embrittlement.
5-25. Quenching from solution heat treating for temperature wrought titanium alloys, except for alloy 3AL-13V-llCr less
than 2 inches thick, which maybe air cooled, shall be by total immersion in water. The water shall be of sufficient volume
or circulation or both so that the water temperature upon completion of the quenching operation will not be more than
100°F. The quenching baths shall be located and arranged to permit rapid transfer of the load from the furnace to the
bath. Maximum quench delay for immersion type quenching shall be 4 seconds for wrought alloys up to 0.091 nominal
thickness and 7 seconds for 0.091 and over. Quench delay time begins when furnace doors begin to open and ends
when the last corner of the load is immersed. With extremely large loads or long lengths quench delay may be exceeded
if performance test indicates that all parts comply with specification requirements.
5-26. AGING AND STRESS RELIEVING . For aging, the material shall be held within temperature range for sufficient
time, depending on section size, for the necessary aging to take place and to insure that specified properties are
developed. Wrought alloys should be fully quenched by air cooling from the aging temperature. The same applies for
stress relieving except the time at temperature will depend on section size plus amount of cold work hardening present in
the material. The material is also quenched by air cooling from the stress relieving temperature.
NOTE
All heat treating operations shall be performed uniformly on the whole part, etc., never on a
portion thereof.
5-4
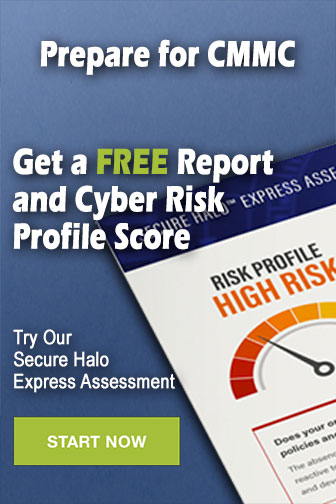