T.O. 1-1A-9
7-10. High speed cutting tools are usually manufactured from the class "T" or class "M" alloys. Four classes, T1, M1, M2
and M10 make up nearly 90% of the general purpose high speed steels. Certain special purpose steels in each class,
such as T6, T7, T8 and T15 are advantageous for operations like milling cutters and pre-hardened forging die blocks.
7-11. High speed drills should possess high strength and toughness, notably M1, M2, M10 and T1. Classes T1 and Ml
are used for tools subject to shock, while M2 and M10 are generally used where tools require less toughness and more
abrasion resistance.
7-12. Material for reamers should be of high hardness and abrasion resistance, such as M1, M2, M10 and T1. The M3
and M15 and T15 classes possess greater abrasion resistance than the lower-vanadium grades.
7-13. Material for taps is generally of the M1, M2 or M10 types. In tapping heat-resisting alloys or steels harder than
Rockwell C35, M15 or T15 may be justified.
7-14. Milling cutters are usually made from the high speed steels. As the hardness of the work piece increases beyond
Rockwell C35, the cobalt high speed steels should be used.
7-15. Recommended punch and die material for blanking parts from 0.050 inch sheet materials are shown in following
table. This table does not cover all operations, and is a sample table intended for use as a guide only:
7-16. HEAT TREAT DATA
7-17. The thermal treatments listed in table 7-5 cover the generally used treatments for the forgings, normalizing, and
annealing of tool and die steels. The thermal treatments listed in table 7-7 cover the usual ranges of temperatures for
hardening and tempering tool and die steels. These tables are listed for use as a guide only, and test samples should be
checked prior to use.
7-18. DISTORTION IN TOOL STEELS Distortion is a general term encompassing all dimensional changes; the two main
types being volume change or change in geometrical form. Volume change is defined as expansion or contraction and
geometric change is defined as changes in curvature or angular relations. Table 7-4 shows an approximate range of size
changes depending upon the type of tool steel, and also dependent on specific tempering and heat treatments. If a very
close tolerance is required for a finished tool, specific data covering this item should be obtained from a detailed source.
7-19. WELDING OF TOOL STEELS
7-20. Compared to other carbon steels, tool steels are relatively difficult to weld.
7-21. GAS WELDING. In the lower carbon ranges, gas welding of tool steels presents no great welding difficulties.
Welding rods should contain a carbon content at least equal the base metal and when hardened and tempered should
have approximately the same physical characteristics.
7-22. SHIELDED METAL - ARC WELDING. Because of the heat effects of arc welding, this process is seldom used for
tool steels. If welding is required one of the following procedures is recommended:
a.
After annealing, preheat the parts and weld with a suitable shielded arc-electrode; then heat treat to restore the
desired properties.
b.
Preheat the parts and use an austenitic electrode.
7-23. PRESSURE GAS WELDING - Drills and other machining tools are frequently welded to less expensive steels.
Use of pressure welds are made at relatively low temperatures in order that no harm may occur to the tool steel that
cannot be removed by subsequent heat treatment. In welds of this nature heat treatment is usually required. Pressure
cycles used on steels vary with the materials, tool steels requiring much high pressure cycles than low carbon steels.
NOTE
See paragraph 2-117, welding STEEL (General).
7-6
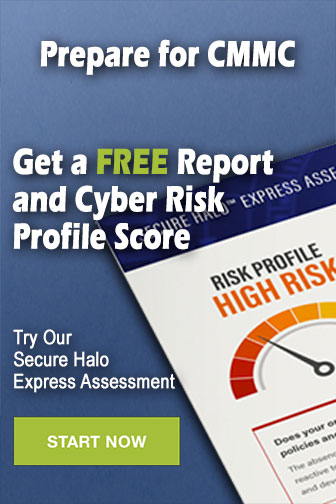