T.O. 1-1A-9
SECTION VII
TOOL STEELS
7-1. GENERAL
7-2. Tool steels are essential to the fabrication of aircraft parts. It is therefore necessary to provide guidance in the
handling of these important metals.
7-3. Tool steels are produced and used in a variety of forms. The more common forms are bars, (round, square,
hexagonal, or octagonal), drill rods, (round, square, or rectangular), flats, and forged shapes.
7-4. ALLOYING ELEMENTS IN TOOL STEELS. (See Table 7-2, chemical composition table.)
a. CARBON - Carbon is the most important single element in tool steel. Changing the carbon content a specific
amount will change the physical properties a greater degree than the same amount of any other element. Degree of
hardness of tool steel quenched from a suitable temperature is a function of carbon content alone.
b. CHROMIUM - In amounts up to 1.80% the addition of chromium produced a marked increase in the hardenability
(depth of hardness) of steels. Small amounts of chromium toughens the steel (greater impact strength), and increases its
strength. Machinability decreases as chromium increases. The addition of 5 to 15% chromium imparts hardening
qualities to the steel. A degree of red hardness and resistance to wear and abrasion results from the addition of
chromium to steel.
c. COBALT - Cobalt is sometimes used in high speed tools. Addition of 5 to 8% increase the red hardness of these
steels.
d. MANGANESE - This element is present in all steels. In amounts of less than 1/2%, it acts as a deoxidizer and
desulfurizer. In amounts greater than 15% it gives steel air hardening tendencies. In intermediate amounts it is
necessary to have other alloying agents present with manganese because of its tendency to make the steel brittle.
e. MOLYBDENUM - Always used in conjunction with other alloying elements, molybdenum acts as an intensifier. It
improves the deep hardening and elevated temperature properties of steel.
f. NICKEL - Nickel makes the steel more ductile. It is used in only a few applications and only in small amounts.
g. SILICON - This element is present in all steels. In amounts of 1/4 to 1% it acts as a deoxidizer. Silicon is added
to shock resisting and hotwork steels to improve their impact characteristics and hardenability. It has a graphitizing
influence and usually requires the addition of carbide stabilizing elements such as molybdenum and chromium.
h. TUNGSTEN - One of the most important features of tungsten steels is their high redhardness. Tungsten steels
are fine grained and high strength, which means they hold good cutting edges. Tungsten content is usually 5 - 12% in
heat resisting tool steels, 4 - 9% in tungsten molybdenum high speed steels, and 14 - 20% in straight tungsten high speed
steel.
j. VANADIUM - This element forms stable carbides and has considerable effect on the hardenability of steels.
Undissolved vanadium carbides inhibit grain growth and reduce hardenability. Dissolved carbides increase hardenability.
Vanadium is also used as a deoxidizer. It is added to plain carbon tool steels to make them fine grained and tough. It is
added to high speed and hot working steels to resist grain growth and help maintain their hardness at elevated
temperatures.
7-5. SPECIFICATIONS. The armed services procure tool steels under three different Federal Specifications, dependent
upon its intended use. Table 7-1 lists these specifications, and present and past classification of the tool steels. Army
Specification 57-108A was superseded by three Army Ordnance Specification's QQ-8-778, QQ-8-779, and QQ-S-780.
which were then superseded by Federal Specification's QQ-T-570, QQ-T-580 and QQ-T-590 respectively.
7-1
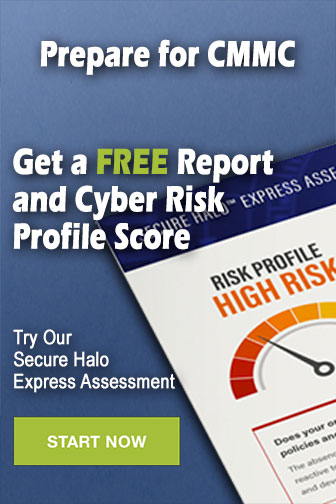