T.O. 1-1A-9
TABLE 7-3. TOOL STEEL SELECTION
7-6. CLASS DESIGNATIONS.
W - Water hardening tool steels
S - Shock resisting tool steels
O - Cold work tool steels, oil hardening types
A - Cold work tool steels, air hardening types
7-7. APPLICATIONS OF TOOL STEELS
7-8. The majority of tool steel applications can be divided into a small number of groups: cutting, shearing, forming,
drawing, extrusion, rolling and battering. Cutting tools include drills, taps, broaches, hobs, lathe tools, etc. Shearing
tools include shears, blanking and trimming dies, punches, etc. Forming tools include draw, forging, cold heading and
die casting dies. Battering tools include chisels and all forms of shock tools. Most cutting tools require high hardness,
high resistance to the softening effect of heat, and high wear resistance. Shearing tools require high wear resistance and
fair toughness. Forming tools must possess high wear resistance or high toughness and strength. In battering tools, high
toughness is most important.
7-9. SELECTION OF MATERIAL FOR A CUTTING TOOL. The selection of material for a cutting tool depends on
several factors: the metal being machined, nature of cutting operation, condition of the machine tool, machining practice,
size and design of tool, coolant to be used, and cost of tool material. Selection is usually based more on previous
experience or applications than on an engineering or metallurgical analysis.
TABLE 7-4. Tool steel Hardening And Tempering Temperatures
7-5
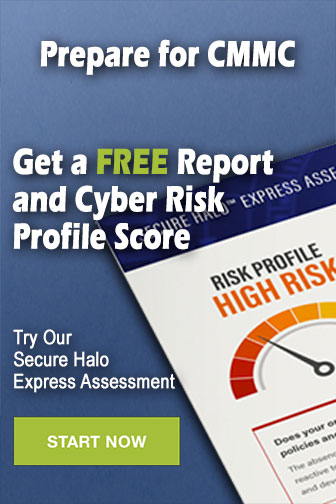