T.O. 1-1A-9
SECTION V
TITANIUM AND TITANIUM ALLOYS.
5-1. CLASSIFICATION.
5-2.
Titanium is produced in pure form as well as in various alloys. Pure titanium is commonly known as unalloyed. It
can be cast, formed, joined, and machined with relative ease as compared to the various alloy grades. Unalloyed
titanium cannot be he; t treated. Therefore, its uses are limited to end items not requiring the higher strengths obtained
from the heat treatable alloys.
5-3.
Titanium is a very active metal, and readily dissolves carbon, oxygen, and nitrogen. The most pronounced effects
are obtained from oxygen and nitrogen. For this reason, any heating process must be performed in a closely controlled
atmosphere to prevent the absorption of oxygen and nitrogen to a point of brittleness.
5-4.
GENERAL
5-5.
MILITARY AND COMMERCIAL DESIGNATIONS . There are presently two military specifications in existence
(See Table 5-1) covering alloyed and unalloyed titanium in classes established to designate various chemical
compositions. For the selection of the proper class and form of stock required for a particular purpose, reference will be
made to Table 5-1.
5-6.
PHYSICAL PROPERTIES. Limited physical properties are available on the titanium compositions covered by
existing military specifications. Compared to other materials, the melting point of titanium is higher than that of any of
the other construction materials currently in use. The density of titanium is intermediate to aluminum and steel.
Electrical resistivities of titanium are similar to those of corrosion resistant steel. The modulus of elasticity is somewhat
more than half that of the alloy steels and the coefficient of expansion is less than half that of austenitic stainless steels.
5-7.
MECHANICAL PROPERTIES . As previously pointed out, titanium is a very active metal and readily dissolves
carbon, oxygen and nitrogen. All three elements tend to harden the metal; oxygen and nitrogen having the most
pronounced effect.
5-8.
The control of these elements causes considerable difficulty in obtaining correct mechanical properties during the
fabrication of titanium. This variation in mechanical properties is the cause of difficulties encountered in the fabrication
of parts, since the absorption of small amounts of oxygen or nitrogen makes vast changes in the characteristics of this
metal during welding, heat treatment, or any application of heat in excess of 800°F.
5-9.
Operations involving titanium requiring the application of heat in excess of 800°F must be performed in a closely
controlled atmosphere by methods explained in future paragraphs. The nominal mechanical properties are listed in
Table 5-2.
5-10. METHODS OF IDENTIFICATION . Methods of distinguishing titanium alloys from other metals are simple and
definite. One quick method is to contact the titanium with a grinding wheel. This results in a pure white trace ending in a
brilliant white burst.
Also, identification can be accomplished by moistening the titanium and marking the surface with a piece of glass. This
leaves a dark line similar in appearance to a pencil mark. Titanium is non-magnetic. To positively identify the various
alloys, a chemical or spectrographic analysis is necessary.
5-11. HARDNESS TESTING. Hardness is the resistance of a metal to plastic deformation by penetration, indentation, or
scratching, and is usually a good indication of strength. This property can be measured accurately by the Brinell,
Rockwell or Vickers Technique. The hardness to be expected from the various alloys and unalloyed titanium is listed in
Table 5-2.
5-12. TENSILE TESTING . The useful strength of a metal is the maximum load which can be applied without permanent
deformation. This factor is commonly called yield strength. The tensile strength of a metal is that load, in pounds per
square inch, at which complete failure occurs. In the case of titanium the yield strength is the most important factor and
is therefore used by industry to designate the various types of unalloyed titanium.
5-13. NON-DESTRUCTIVE TESTING . Titanium and titanium alloys are highly susceptible to stress risers resulting from
scratching, nicking, and notching. For this reason, close visual inspection is required of all raw stock prior to any forming
or machining operations. All scratches, nicks and notches must be removed, before fabrication, by sanding and
polishing.
5-14. and 5-15. Deleted.
Change 4
5-1
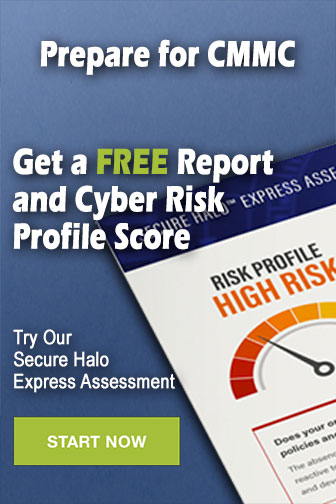