TM 1-1510-225-10
2-61
c. Engine Instruments F3 . Engine instru-
ments, located on the left of the center position of the
instrument panel, are grouped according to their
function. At the top, the ITT indicators and
torquemeters are used to set takeoff power. Climb
and
cruise
power
are
established
with
the
torquemeters
and
propeller
tachometers
while
observing ITT limits. Gas generator (N1) operation is
monitored by the gas generator tachometers. The
lower grouping consists of the fuel flow indicators and
the oil pressure/temperature indicators.
(1) The ITT indicator gives an instantaneous
reading of engine gas temperature between the
compressor turbine and the power turbines. This ITT
reading is self-generating.
(2) The torquemeters give an indication of
foot-pounds of torque being applied to the propeller.
The instruments are powered by 26 Vac power
through the left and right torquemeter circuit breakers
respectively, located on the right side panel.
(3) The N1 or gas generator tachometer is
read in percent of RPM, based on a figure of
37,500 RPM at 100%. Maximum continuous gas
generator speed is limited to 38,100 RPM or 101.5%
N1. Both readings are self-generating.
(4) Oil
pressure
and
temperature
are
indicated on two gauges, one for the left engine oil
pressure and temperature and an identical gauge for
the right engine. These dc gauges are powered by the
No. 1 and No. 2 dual feed buses respectively, and are
protected by 5-ampere circuit breakers, placarded OIL
PRESS and OIL TEMP, located on the right sidewall
circuit breaker panel.
(5) Two gauges indicate the rate of flow for
consumed fuel as measured by sensing units coupled
into the fuel supply lines for each engine. The fuel flow
indicators are calibrated in increments of hundreds of
pounds per hour. The left engine indicator is powered
by the No.1 dual feed bus and the right is powered by
the No, 2 dual feed bus. Both indicators are protected
by 5-ampere circuit breakers, placarded FUEL FLOW,
located on the right sidewall circuit breaker panel.
Proper observation and interpretation of these
instruments
provide
an
indication
of
engine
performance and condition.
2-31. ENGINE TREND MONITOR.
a. General Description. The Engine Trend
Monitor (ETM) is a monitoring system that monitors
and records data on engine and airframe parameters,
e.g., fuel used, cycle counts, total hours, and engine
and airframe exceedences. It provides automatic
cycle and engine start counting and automatic data
collection. The ETM provides maintenance personnel
with a complete, accurate, and detailed record of the
engine and airframe use. At the time of first
installation of the ETM in the aircraft, the data in the
ETM is revised with the current pertinent statistical
data concerning the airframe and engines. The ETM
can also serve as a log that will contain detailed
records of each event in a flight from power on, engine
starts to engine stops, and power off.
NOTE
When the ETM system is inoperative, pilots
are responsible for manually recording
engine trend data.
b. System and Related Components.
(1) The ETM Processor. The processor
contains the main computer, and is the collection point
for data received from the various engine transducers.
(2) The Airdata Computer. T3 F3 The
Airdata computer provides airdata calculations and is
interfaced to the KLN90B GPS receiver. R The
Airdata computer provides airdata calculations and is
the interface to the GNS -XLS FMS.
(3) The Display & Key Recorder. The
Display and Key Recorder is a cabin-mounted display
that houses both the key recorder equipment and
display interface.
(4) Indicator Light. An indicator light, labeled
ETMS, is located on the right side of the instrument
panel below the stormscope. The ETMS indicator light
illuminates when the ETM is recording data and for
10 seconds after the master switch is turned on.
c. Normal Operations. When the master
switch is turned on, power is applied to the ETM
causing the ETMS indicator light to illuminate and the
ETM to perform a self-test. It is vital that the pilot
follow certain procedures when starting up and
shutting down the aircraft in accordance with the
following:
(1) When starting the aircraft, wait a full
10 seconds before starting the engines after turning on
the master switch to allow the ETM to complete its
startup procedures.
(2) If the engines are started before the ETM
has completed its startup sequence, the system will
not record any engine starts. This will result in
inaccurate cycle counts, engine start counting, and
trend analysis.
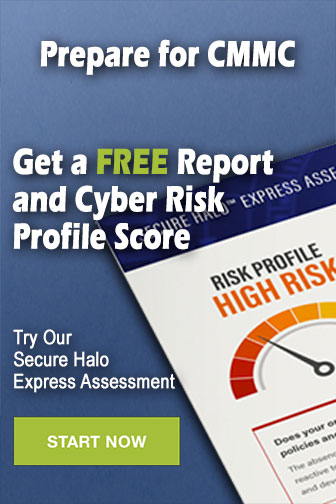