TM 1-1510-225-10
2-62
(3) When shutting down the engines, wait
until the gas generator speeds of both engines drop
below 10% prior to turning off the master switch.
(4) During
aircraft
operation,
the
ETM
monitors and records data on the engine and airframe
parameters and notifies maintenance personnel when
the established limits of those parameters are
exceeded. This data is, in turn, used for later trend
analysis. The ETM has a secure feature that prevents
unauthorized changes to the retained statistical data
being recorded.
Section IV. FUEL SYSTEM
2-32. FUEL SUPPLY SYSTEM.
The engine fuel supply system, Figure 2-18,
consists of two separate but identical systems sharing
a common fuel management panel, Figure 2-19, and
fuel crossfeed plumbing, Figure 2-20. Each main fuel
system consists of five interconnected wing tanks and
a nacelle tank. Each auxiliary fuel system consists of
one tank located between the nacelle and the
fuselage. A fuel transfer pump is located within each
auxiliary tank. Additionally, the system has an engine-
driven boost pump, a standby fuel pump located within
each nacelle tank, a fuel heater (engine oil-to-fuel heat
exchanger unit), a tank vent system, tank vent heating
system, and interconnecting wiring and plumbing.
Total fuel tank capacity is shown in Table 2-2. Gravity
feed fuel flow is shown in Figure 2-21.
a. Fuel Tanks. The main wing tanks consist of
two leading edge tanks, two box section bladder tanks,
and an integral (wet cell) tank all interconnected to
flow into the nacelle tank by gravity. This system of
tanks is filled from the filler located near the wing tip.
The auxiliary fuel system consists of a center section
tank, located in the inboard wing, with its own filler
opening and an automatic fuel transfer system to
transfer the fuel into the nacelle tank. An anti-siphon
valve is installed at each filler port to prevent loss of
fuel or collapse of a fuel cell bladder in the event of
improper securing or loss of the filler cap. The nacelle
tank is located directly behind the engine and contains
a submerged, electrically operated standby fuel pump.
The fuel from the nacelle tank is fed directly into the
engine by either the engine-driven primary fuel pump
or, as backup, the standby fuel pump. The quantity of
fuel for the tanks is detailed in Table 2-3.
b. Engine-Driven Boost Pumps. A gear-driven
boost pump mounted on each engine, supplies fuel,
under pressure, from the nacelle tank to the inlet of the
engine-driven primary high-pressure pump for engine
starting and all normal operations. Either the engine-
driven boost pump or electric standby pump is capable
of supplying sufficient pressure to the engine-driven
primary high-pressure pump, maintaining normal
engine operation.
CAUTION
Engine operation using only the engine-
driven primary (high-pressure) fuel pump
without standby pump or engine-driven
boost pump fuel pressure is limited to 10
cumulative hours.
NOTE
This condition is indicated by illumination
of both the L or R FUEL PRESS warning
annunciator
and
the
simultaneous
illumination of both MASTER WARNING
annunciators. All time in this category
shall be entered on DA Form 2408-13-1 for
the attention of maintenance personnel.
c. Standby Fuel Pumps. A submerged,
electrically operated standby fuel pump, located within
each nacelle tank, serves as a backup unit for the
engine-driven boost pump. The standby pumps are
switched off during normal system operations. A
standby fuel pump will be operated during crossfeed
operation to pump fuel from one nacelle tank to the
opposite engine. Each standby fuel pump has an
inertia switch included in the power supply circuit.
When subjected to a 5 to 6 G shock loading, as in a
crash situation, the inertia switch will remove electrical
power from the standby fuel pumps. The standby fuel
pumps are protected by two 10-ampere circuit
breakers, placarded LEFT or RIGHT STANDBY
PUMP, located on the left sidewall circuit breaker
panel, and four 5-ampere circuit breakers (two each in
parallel) on the hot battery bus.
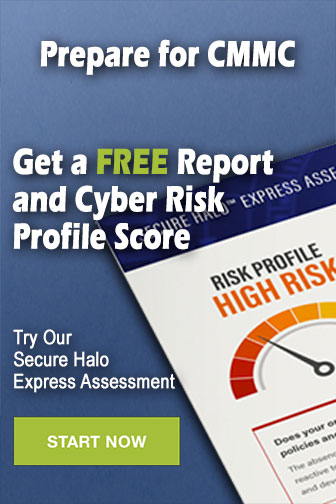