TM 1-1510-225-10
2-43
2-22. CONDITION LEVERS.
The two CONDITION levers are located on the
control pedestal. Each lever starts and stops the fuel
supply, and controls the idle speed for its respective
engine. The levers have three placarded positions:
FUEL CUTOFF, LOW IDLE, and HIGH IDLE. In the
FUEL CUTOFF position, the CONDITION lever
controls the cutoff function of its engine-mounted fuel
control unit. From LOW IDLE to HIGH IDLE, they
control the governors of the fuel control units to
establish minimum fuel flow levels. LOW IDLE
position sets the fuel flow rate to attain approximately
61% N1 and HIGH IDLE position sets the rate to attain
approximately 70% N1. The POWER lever for the
corresponding
engine
can
select N1
from
the
respective idle setting, up to maximum power. An
increase in low idle N1 will be experienced at high field
elevation.
2-23. FRICTION LOCK KNOBS.
Friction drag of the engine and propeller control
leve rs is adjusted, as applicable, by four friction lock
knobs. The friction lock knobs, placarded FRICTION
LOCK, are located on the control pedestal. One knob
is below the propeller levers, one is below the
CONDITION levers, and two are below the POWER
leve rs. When a knob is rotated clockwise, the friction
increases opposing movement of the affected lever as
set by the pilot. Counterclockwise rotation of the knob
will decrease friction, thus permitting free and easy
lever movement.
2-24. ENGINE FIRE DETECTION SYSTEM.
a. Description R . A fire detection system is
installed to provide an immediate warning in the event
of
a
fire
or
overtemperature
in
each
engine
compartment. Refer to Figure 2 -12. The system
consists of a temperature sensing cable for each
engine, two red warning annunciators, a test switch on
the copilot's left subpanel, and a 5-ampere circuit
breaker, placarded FIRE DET on the right sidewall
circuit breaker panel. The test switch, placarded TEST
SWITCH ENG FIRE SYS EXT R / L and DET R / L, is
located on the copilot's subpanel. When the test
switch is placed in the DET L or R position, the
corresponding L ENG FIRE
or R ENG FIRE
annunciator on the warning annunciator panel and the
MASTER WARNING annunciators will illuminate and
flash.
NOTE
The system may be tested on the ground
or in flight.
When a fire has been extinguished, if the
integrity of the system has not been destroyed, the
system will reset itself.
b. Description T3 F3 OSA . A pneumatic fire
detection system, Figure 2-13, is installed to provide
an immediate warning in the event of a fire or over-
temperature in the engine compartment. The main
element of the system is a temperature sensing cable
routed
continuously
throughout
either
engine
compartment, terminating in a responder unit. The
responder unit is mounted in each engine accessory
area on the upper left hand engine truss just forward of
the engine firewall. The responder unit contains two
sets of contacts: a set of integrity switch contacts for
continuity test functions of the fire detection circuitry,
and a set of alarm switch contacts which completes
the circuit to activate the fire warning system when the
detector cable senses an over-temperature condition
in critical areas around the engine.
The sensor cable consists of an outer tube filled
with an inert gas, and an inner hydride core that is
filled with an active gas. The gases within the tube
form a pressure barrier that keeps the contacts of the
responder integrity switch closed for fire alarm
continuity test functions. As the temperature around
the sensing cable increases, the gases within the tube
begin to expand. When the pressure from the
expanding gases reaches a preset point, the contacts
of the responder alarm switch close, causing the
respective
ENG FIRE annunciator and flashing
MASTER WARNING lights to illuminate.
The fire warning system consists of two red
lenses placarded L ENG FIRE and R ENG FIRE,
located in the warning annunciator panel, two red
MASTER WARNING lights located on opposite sides
of the glareshield, and two responder units with
pneumatic sensors in the engine compartments.
An integrity switch that monitors the system is
held in the closed position. If the detector should
develop a leak, the loss of gas pressure would allow
the integrity switch to open and signal a lack of
detector integrity. The system then will not operate
during the system test function.
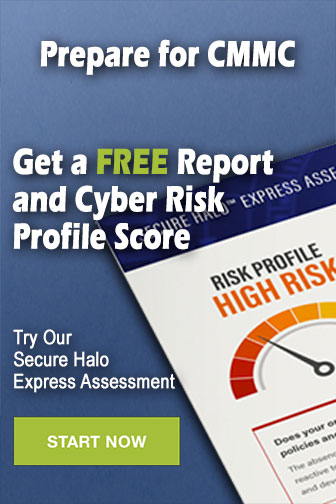