TM 1-1510-225-10
2-76
actuated by the PROP GOV TEST switch, located on
the pilot's subpanel, is provided for resetting the
overspeed
governor
to
approximately
1830
to
1910 RPM for test purposes. If the propeller sticks or
moves too slowly during a transient condition, causing
the propeller governor to act too slowly to prevent an
overspeed condition, the power turbine governor,
contained within the constant speed governor housing,
acts as a fuel topping governor. When the propeller
reaches 106% of selected N2 RPM, the power turbine
governor limits the fuel flow to the gas generator,
reducing N1 RPM, which in turn prevents the propeller
from exceeding approximately 2120 RPM. During
operation in the reverse range, the power turbine
governor is reset to approximately 95% of propeller
RPM before the propeller reaches a negative pitch
angle. This ensures that engine power is limited,
allowing a propeller RPM of somewhat less than that
of the constant speed governor setting to be
maintained. The constant speed governor, therefore,
will always sense an underspeed condition and direct
oil pressure to the propeller servo piston to permit
propeller operation in beta and reverse ranges.
2-44. LOW PITCH STOP.
Low pitch propeller position is determined by a
mechanically monitored hydraulic low pitch stop. The
propeller servo piston is connected to the beta collar
by four spring-loaded sliding rods mounted behind the
propeller. A carbon brush block riding in the beta
collar transfers the movement of the collar through the
propeller-reversing lever to the beta valve of the
governor. The initial forward motion of the beta valve
from its rigged position blocks off the flow of oil to the
propeller. Further motion dumps the oil from the
propeller into the reduction gearbox sump. A
mechanical stop limits the forward motion of the beta
valve. Rearward movement of the beta valve from its
rigged position does not affect normal propeller
control. When the propeller is rotating at a speed
lower than that selected on the governor, the governor
pump provides oil pressure to the servo piston. This
decreases the pitch of the propeller blades until the
feedback of motion from the beta collar pulls the beta
valve into position blocking the supply of oil to the
propeller, preventing further pitch changes.
2-45. GROUND IDLE STOP SYSTEM T3 F3 .
The ground idle stop system, using an electrical
solenoid mounted on the front of the reversing
push/pull cable, is designed to operate on the ground
only by resetting the propeller blades to maintain an
angle below flight idle (from 16° to 10°). The solenoid
is connected to the propeller reversing lever by means
of a slotted clevis which allows the reversing lever to
be pulled aft, resetting the Beta valve.
The electrical solenoid is wired through the right
hand landing gear squat switch and quadrant idle
sense switch. As the aircraft lands, the squat switch
activates the solenoid, which in turn pulls the reverse
lever back to reset the Beta valve. This enables the
propeller blades to reset automatically to a blade angle
lower than the flight idle blade angle increasing
propeller RPM. Propeller RPM on the ground is
restricted for continuous operation to a minimum of
1150 RPM. Ground operation of the propeller in flight
idle blade angle would result in a RPM within the
prohibited RPM range. The travel on the reverse lever
is limited by the slot in the clevis. While the aircraft is
on the ground, the system remains activated. When
the squat switch deactivates the solenoid, the spring
force from the Beta valve pushes the reverse lever
forward to its original position.
2-46. GROUND FINE R .
Lifting the POWER levers and moving them aft
past the flight idle stop will place the POWER levers
into the ground fine position. Approximately halfway
back to the ground fine gate, a mechanical linkage at
the propeller governor will begin to bleed Py air from
the fuel control unit, provided the PROP levers are
positioned to the HIGH RPM position. This results in a
decrease in engine N1, torque, and propeller RPM.
With the POWER levers at the ground fine gate,
engine N1 should be within the range of 62% to 67%,
and propeller RPM should not be less than 1000 RPM.
2-47. PROPELLER SYNCHROPHASER.
a. Description. The propeller synchrophaser
matches left and right propeller RPM as well as
propeller phase relationship. This phase relationship
is designed to decrease cabin noise, and is not
adjustable in flight. A toggle switch, placarded PROP
SYN ON / OFF, installed adjacent to the synchroscope
on the pilot's instrument panel, turns the system on/off.
Signal pulses occurring once per revolution of
the propeller are obtained from magnetic pickups
(located in the front of the engine on the deice brush
mounting bracket) when the target (mounted on the aft
side of the spinner bulkhead) passes the magnetic
pickup. The signal pulses are sent to a control box
installed forward o f the pedestal. The control box
receives these signal pulses and compares them for
pulse rate and relative position. Differences in pulse
rate and/or propeller position cause the control box to
vary the voltage in the primary governor coil, which in
turn increases propeller speed until the correct speed
and phasing are obtained.
A governor coil increases the speed set by the
propeller control lever, but never decreases the speed
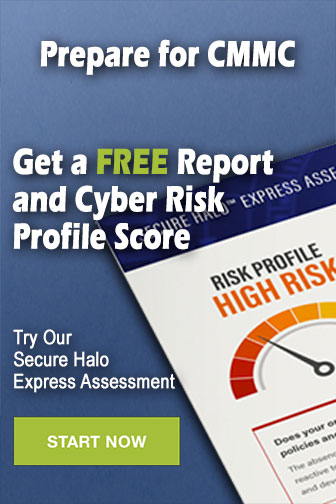