TM 1-1510-225-10
2-128
(2) Use of Kerosene Fuels. The use of
kerosene fuels (JP -5 type) in turbine engines dictates
the need for observance of special precautions. Both
ground starts and air restarts at low temperature may
be more difficult due to low vapor pressure. Kerosene
fuels having a freezing point of 40 °C (-40 °F), limit
the maximum altitude of a mission to 28,000 feet
under standard day conditions.
(3) Mixing of Fuels in Aircraft Tanks. When
changing from one type of authorized fuel to another,
for example JP-8 to JP-5, it is not necessary to drain
the aircraft fuel system before adding the new fuel.
(4) Fuel Specifications. Fuels having the
same NATO code number are interchangeable. Jet
fuels conforming to ASTM D-1655 specification may
be used when MIL-T-83133 fuels are not available.
This usually occurs during cross-country flights where
aircraft using NATO F-34 (JP-8) are refueling with
NATO F-40 (JP-4) or commercial ASTM type B fuels.
Whenever this condition occurs, the engine operating
characteristics may change in that lower operating
temperature, slower acceleration, lower engine speed,
easier starting, and shorter range may be experienced.
The reverse is true when changing from F-40 (JP-4)
fuel to F-34 (JP -8) or Commercial ASTM Type A -l
fuels. Most commercial turbine engines will operate
satisfactorily on either kerosene or JP -4 type fuel. The
difference in specific gravity may possibly require fuel
control adjustments; if so, the recommendations of the
manufacturers of the engine and airframe are to be
followed.
2-91. SERVICING OIL SYSTEM.
An integral oil tank occupies the cavity formed
between the accessory gearbox housing and the
compressor inlet case on the engine. The tank has a
calibrated oil dipstick and an oil drain plug. Avoid
spilling oil. Any oil spilled must be removed
immediately. Use a cloth moistened in solvent to
remove oil. Overfilling may cause a discharge of oil
through the accessory gearbox breather during engine
operation, until a satisfactory level is reached. Service
oil system as follows:
1. Open access door on upper cowling to
gain access to oil filler cap and dipstick.
CAUTION
A cold oil check is unreliable. If possible,
check oil within 10 minutes after engine
shutdown.
If
over
10 minutes
have
elapsed, motor the engine for 40 seconds,
then check. If over 10 hours have elapsed,
start the engine and run for 2 minutes, then
check. Add oil as required. Do not overfill.
2. If oil level is over 2 quarts low, motor or
run engine as required, and service as
necessary.
3. Remove oil filler cap.
4. Insert
clean
funnel,
with
screen
incorporated, into filler neck.
5. Replenish with oil to within 1 quart below
MAX mark or MAX COLD on dipstick (cold
engine). Fill to MAX or MAX HOT (hot
engine).
CAUTION
Ensure that oil filler cap is correctly
installed and securely locked to prevent
loss of oil and possible engine failure.
6. Check oil filler cap for damaged preformed
packing, general condition and locking.
7. Install and secure oil filler cap.
8. Check for any oil leaks.
2-92. SERVICING THE HYDRAULIC SYSTEM.
a. Servicing
Hydraulic
Brake
System
Reservoir.
1. Gain access to brake hydraulic system
reservoir.
2. Remove brake reservoir cap and fill
reservoir to washer on dipstick with
hydraulic fluid.
3. Install brake reservoir cap.
b. Servicing Hydraulic Landing Gear System.
Servicing the hydraulic landing gear extension/
retraction system consists of maintaining the correct
fluid level and maintaining the correct accumulator pre-
charge. The accumulator is located in the reservoir
access area and is charged to 800 ± 50 psi using
bottled nitrogen. A charging gauge is mounted on the
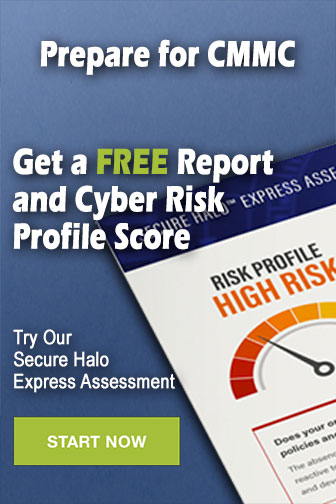