T. O. 1-1A-9
HEAT TREATMENT
For maximum stress-rupture life in range 1560°1740°F, fully heat treat solution treat, and double age as follows: Solution
treat 21020F 4 hours, air cool. Double age 19220F, 16 hours, air cool and 1526°F, 8 hours, air cool. Where stress
rupture strength above 1562OF is not the important property, but tensile strength, elongation and impact strength up to
1292OF is desired, the following heat treatment is recommended.
Solution treat 21040F, 4 hours, air cool.
Age 15620F, 16 hours, air cool.
2-75. MACHINING OF STEELS (GENERAL)
2-76. There are five basic factors affecting machinability as related to steel: They comprise (1) the capacity and rigidity
of the machine tool; (2) cutting fluids; (3) design composition and hardness of the cutting tool; (4) cutting condition with
respect to feeds and speeds; and (5) the structure of the steel to be machined.
2-77. The cutting tool angles (back rake, side clearance, front clearance, and side rake) are highly important in the
machining of metals. The range of values based on general practice for the machining of steel and steel alloys, are as
follows: (1) back rake angle, 8-16 degrees; (2) side rake angle, 12-22 degrees; (3) front clearance angle, 8-13 degrees;
and (4) side clearance angle, 10-15 degrees.
2-78. Regardless of the material of which the cutting tool is made, the cutting action is the same. The main difference is
the cutting speed. The carbon-steel tool cuts at low speed. The high-speed tool cuts at twice the speed of carbon-steel,
the cast alloys at twice the speed of high-speed steel, and the sintered carbides at twice that of the cast alloys. The
cutting speeds listed in Table 2-4 are approximate speeds using high-speed steel tools, and are to be used only as a
basis from which proper speeds for a particular part may be calculated. These speeds are based on SAE 1112 steel,
which is assigned a machin2bility rating of 100%. In order to obtain an approximate starting speed for different steels,
select the type of operation, the width, depth or diameter of cut and obtain the recommended cutting speed for SAE 1112
from Table 2-3 then refer to Table 2-4 for the percent rating of the metal to be machined, and multiply the SFM value
from Table 2-5 by the rating in Table 2-4. The result is the recommended surface feet per minute (SFM) for the cutting
operation. For a known diameter and surface feet per minute (SFM) to be used for an operation, the corresponding
revolution per minute (RPM) can be obtained from Table 2-5.
2-79. The term cutting feed is used to express the axial distance the tool moves in each revolution. A course feed is
usually used for roughing operations, and a fine feed for finishing operations. In general, the feed remains the same for
different cutting tool steels, and only the speed is changed. Approximate cutting feeds are listed in Table 2-3. For tool
corrections when improper machining on an operation is encountered, refer to Table 2-6 for recommended checks.
2-80. The use of a proper coolant (cutting fluid) often results in an increase of cutting speed for the same tool life, and
also acts as a lubricant giving better cutting action and surface finish. Recommended cutting fluids for steels are lard oil,
mineral oils, sulphurized oils, and soluble or emulsifiable oils.
2-66
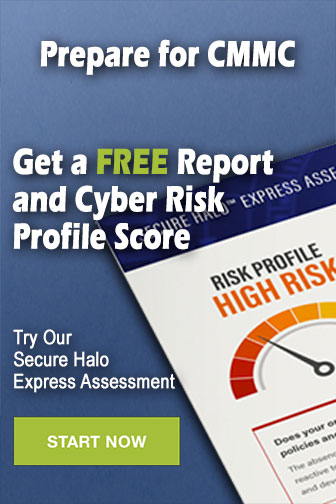